ثلاثة أخطاء شائعة عند شراء مصبوبات صمام الكرة
مرحباً بكم في مدونتي!
I’m thrilled to have you here! Before we dive into the content, I’d love for you to join me on my social media platforms. It’s where I share extra insights, connect with our amazing community, and keep you updated on the latest news. Here’s how you can stay connected:
📘 Facebook: Shanghai Leierwo Industry Trade Co., Ltd.
Now, let’s embark on this journey together! I hope you find the content here not only insightful but also inspiring and valuable. Let’s get started!
جدول المحتويات
مقدمة
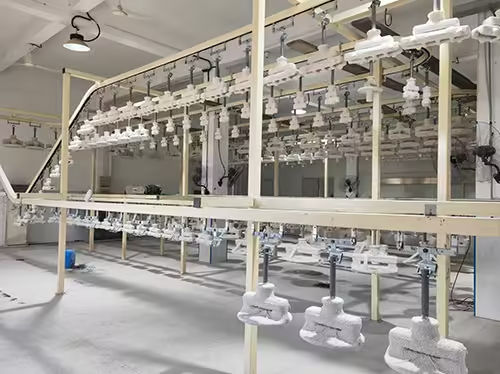
Purchasing globe valve castings requires careful consideration of multiple factors to ensure optimal performance and longevity. Many buyers, however, make critical errors that lead to premature failures, operational inefficiencies, and unnecessary costs. This comprehensive guide examines three common mistakes when buying globe valve castings and provides expert recommendations to help you make informed purchasing decisions.
Whether you’re sourcing globe valve castings for oil and gas applications, power plants, or industrial processing systems, understanding these pitfalls will help you avoid costly errors and select components that meet your exact requirements.
Mistake 1: Ignoring Material Compatibility
One of the most frequent errors when purchasing globe valve castings is failing to properly evaluate material compatibility with the intended service conditions. Globe valve castings must withstand specific temperatures, pressures, and corrosive environments, yet many buyers focus solely on initial cost rather than long-term performance.
Key Material Considerations for Globe Valve Castings
Material Grade | Temperature Range | Pressure Rating | مقاومة التآكل | Typical Applications |
---|---|---|---|---|
WCB Carbon Steel | -29°C to 425°C | Class 150-2500 | معتدل | Water, steam, oil |
CF8M Stainless | -196°C to 800°C | Class 150-2500 | ممتاز | Chemical, marine |
WC6 Alloy Steel | -29°C to 593°C | Class 150-2500 | جيد | High temp steam |
C95800 Bronze | -198°C to 260°C | Class 150-600 | ممتاز | Marine, seawater |
When selecting globe valve castings, always consider:
- Chemical composition of the process fluid
- Maximum and minimum operating temperatures
- System pressure fluctuations
- Potential for erosion or cavitation
Mistake 2: Overlooking Quality Certifications
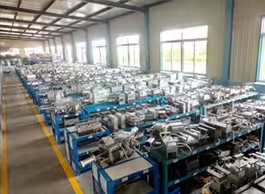
Another critical mistake that many make when selecting globe valve castings is neglecting to verify the manufacturer’s quality certifications and testing protocols. Globe valve castings are pressure-retaining components, which means they play a vital role in ensuring the safety, efficiency, and reliability of any system. These components need to be subjected to rigorous quality control standards throughout the production process.
Essential certifications to look for in globe valve castings suppliers include:
- ISO 9001:2015 for Quality Management Systems:This certification ensures that the supplier follows internationally recognized standards for managing product quality throughout the manufacturing process. It focuses on continuous improvement and customer satisfaction.
- PED 2014/68/EU for European Market Compliance:The Pressure Equipment Directive (PED) ensures that the supplier’s products meet European Union standards for pressure equipment. This certification is critical if your globe valve castings will be used in the European market or in applications that involve high-pressure systems.
- ASME B16.34 for Valve Design and Manufacturing Standards:The American Society of Mechanical Engineers (ASME) B16.34 standard specifies the requirements for valve design, materials, and pressure-temperature ratings. This certification indicates that the globe valve castings are designed to meet high standards of durability and performance.
- NACE MR0175 for Sour Service Applications:If the globe valve castings are to be used in corrosive environments, such as in the oil and gas industry, it is important to verify compliance with NACE MR0175. This certification ensures the materials can withstand sour service conditions, including exposure to hydrogen sulfide.
What Reputable Manufacturers Should Provide
A reputable manufacturer of globe valve castings should provide comprehensive documentation to demonstrate the quality of their products. Some of the essential documents to expect include:
- Material Test Reports with Full Chemical Analysis
These reports detail the chemical composition of the materials used in the valve castings, ensuring they meet the required specifications for strength, corrosion resistance, and other properties. - Mechanical Property Test Results
These test results give insights into the material’s mechanical properties, such as yield strength, tensile strength, hardness, and ductility. For example, when using materials like 1020 steel, the yield strength can significantly affect the durability of the globe valve castings. - Non-Destructive Examination Reports
Non-destructive testing (NDT) methods like ultrasonic testing or radiography should be used to identify internal flaws in the valve castings. These reports help ensure the integrity of the castings before they are put into service. - Pressure Test Certificates
Pressure testing ensures that the valve castings can withstand the pressure they will be subjected to during operation. This test is essential for verifying the safety and functionality of the components.
Mistake 3: Focusing Only on Initial Cost
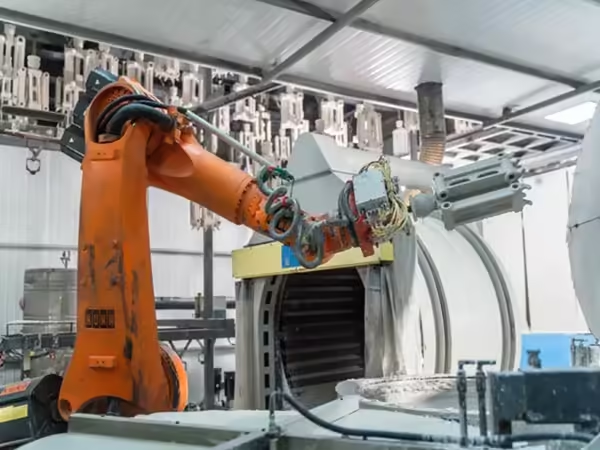
Another common mistake is basing purchasing decisions solely on the initial cost. While low-priced options might seem appealing, they often result in higher long-term expenses due to maintenance, replacements, and inefficiencies.
Factors affecting the true cost of globe valve castings include:
- Expected Service Life Under Operating Conditions: Low-cost products may wear out more quickly, leading to frequent replacements. High-quality options offer longer service life, reducing the need for replacements and minimizing downtime.
- Maintenance Requirements and Downtime Costs: Valves that require frequent repairs or servicing can lead to significant downtime costs. Choosing durable components can minimize these maintenance needs.
- Energy Efficiency Considerations: Valves that offer better flow characteristics can help reduce energy consumption, providing operational savings over time.
- Availability of Replacement Parts: Some suppliers may not offer readily available spare parts, increasing the cost of maintaining your system. Opting for a supplier with accessible parts reduces the overall lifecycle cost.
Premium globe valve castings typically offer:
While premium options often come with a higher initial price tag, the benefits they offer in the long run make them a worthwhile investment:
- Longer Service Intervals
Higher-quality materials and design lead to longer intervals between replacements, reducing overall maintenance costs. - Reduced Leakage Rates
A well-designed valve will have better sealing performance, reducing leakage and improving system efficiency. - Better Flow Characteristics
Premium products often offer better flow dynamics, which can enhance system performance and reduce energy consumption. - Lower Lifecycle Costs
Investing in high-quality components helps reduce maintenance needs, extending the life of the system and lowering overall costs.
How to Avoid These Mistakes
To select the right valve components for your application, take the following steps:
- Consult with Materials Engineers
Work with experts to understand the specific requirements of your application, ensuring the material used is suitable for your operational environment. - Request Detailed Documentation
Always ask for certifications, test results, and inspection reports to verify the quality of the components you’re purchasing. - Evaluate Multiple Quotations
Look at more than just the initial price. Request detailed cost breakdowns, including maintenance, energy usage, and part replacement costs, to get a true sense of the total cost of ownership. - Consider Prototype Testing for Critical Applications
For high-pressure or complex environments, test a prototype to ensure the product meets your performance expectations before committing to large-scale orders. - Establish Long-Term Supplier Relationships
By partnering with reliable suppliers, you ensure continuous support, access to quality products, and assistance with any future needs or upgrades.
خاتمة
Avoiding these three common mistakes when buying globe valve castings can significantly improve system reliability, reduce maintenance costs, and extend equipment lifespan. By focusing on material compatibility, quality certifications, and total cost of ownership rather than just initial price, you’ll make smarter purchasing decisions that pay dividends throughout the valve’s service life.
Remember that globe valve castings are critical components in any fluid handling system, and cutting corners during the selection process often leads to operational problems down the line. Invest time in proper evaluation and consultation with experts to ensure optimal performance from your valve components.
الأسئلة الشائعة
What is the most durable material for globe valve castings?
The most durable material for globe valve castings depends on the specific application conditions. CF8M stainless steel offers excellent corrosion resistance and is ideal for chemical processing or water treatment applications, while WC6 alloy steel is better suited for high-temperature environments, such as power plants and refineries. For applications requiring a balance of strength and corrosion resistance, F51 duplex stainless steel is a good choice, while carbon steel offers durability at a lower cost in less demanding situations.
How can I verify the quality of globe valve castings?
To verify the quality of globe valve castings, request material test reports that provide chemical analysis to confirm the composition of the material. Ensure that mechanical properties, including tensile strength and hardness, meet required standards. Inspection certificates that include non-destructive examination (NDE) results like ultrasonic testing or X-rays are also essential. Additionally, performance data regarding pressure ratings and temperature tolerance, along with third-party inspection services, can help validate the casting’s quality.
Why do some globe valve castings fail prematurely?
Premature failure of globe valve castings is often caused by material incompatibility, such as using a material that cannot withstand the operational conditions like extreme temperatures or corrosive substances. Manufacturing defects like cracks, porosity, or voids can weaken the casting, while operation beyond the valve’s design parameters (e.g., excessive pressure or temperature) can lead to failure. Improper installation or maintenance neglect can also contribute to early failures, as can wear and tear over time.
What’s the typical lead time for custom globe valve castings?
Lead time for custom globe valve castings depends on factors like material type and design complexity. For standard materials, the lead time is typically between 8 to 12 weeks, including production and shipping. For specialized alloys or custom designs, lead time can extend to 14 to 20 weeks, as these require additional sourcing of materials and more complex manufacturing processes. Always confirm the estimated lead time with the manufacturer before placing an order.
How often should globe valve castings be inspected?
The frequency of inspections for globe valve castings depends on the application’s criticality. In high-stress applications such as power generation, oil and gas, or chemical processing, annual inspections are typically recommended. For less demanding conditions, inspections every 2 to 3 years may suffice. It is essential to follow the manufacturer’s recommended inspection schedules and adjust based on the operational environment to ensure the valve’s reliability and longevity.
فئات المنتجات
- أجزاء الصمامات
- أجزاء مضخة المياه
- أجزاء صندوق المحمل
- أجزاء الصب بالقالب
- منتجات مضخات الفولاذ المقاوم للصدأ
- منتجات مضخات الحديد الزهر
- قطع غيار الصمامات لاستخدام السيارات
- قطع غيار السيارات
- أجزاء الصمامات للاستخدام المدني
- قطع غيار مضخة التفريغ KF
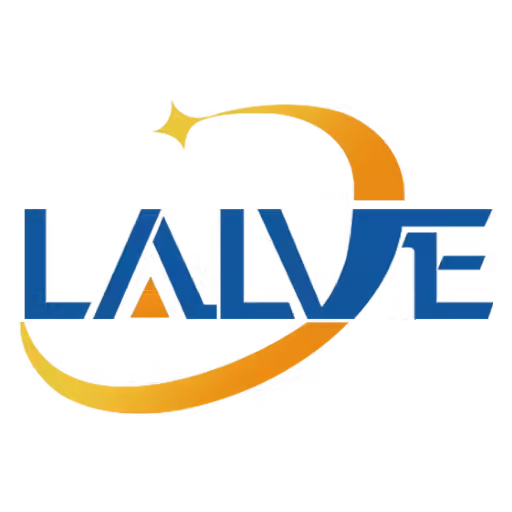