Avoid 5 Common Mistakes with High Pressure Valve Castings
Willkommen auf meinem Blog!
Ich freue mich sehr, dass du hier bist! Bevor wir uns in die Inhalte vertiefen, würde ich mich freuen, wenn du mir auf meinen Social-Media-Plattformen folgst. Dort teile ich zusätzliche Einblicke, vernetze mich mit unserer großartigen Community und halte dich über die neuesten Nachrichten auf dem Laufenden. So bleibst du in Verbindung:
📘 Facebook: Shanghai Leierwo Industriehandel Co., Ltd.
Lassen Sie uns gemeinsam auf diese Reise gehen! Ich hoffe, Sie finden die Inhalte hier nicht nur aufschlussreich, sondern auch inspirierend und wertvoll. Los geht‘s!
Inhaltsverzeichnis
Einführung
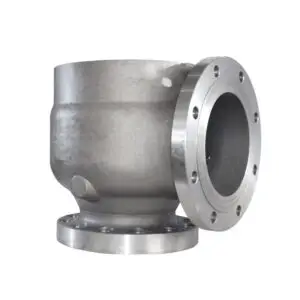
High pressure valve castings play a crucial role in various industries, particularly in sectors requiring heavy-duty valves for controlling the flow of liquids and gases under high pressure. These castings are used in applications ranging from oil and gas pipelines to chemical processing plants, making them integral to operational efficiency and safety. However, while high pressure valve castings offer excellent performance, they are not without their challenges. In this article, we’ll explore common mistakes people make with high pressure valve castings and how to avoid them.
Understanding High Pressure Valve Castings
Before diving into the mistakes to avoid, it’s essential to understand what high pressure valve castings are. High pressure valve castings are made by pouring molten metal into a mold to form parts used in high-pressure valves. These valves are designed to handle extreme pressures without compromising functionality. The materials used for these castings are typically steel or specialized alloys designed for strength and durability.
Key Features
High pressure valve castings have specific characteristics that make them ideal for applications that deal with high pressure. Some of these key features include:
- Durability: High pressure valve castings are designed to withstand intense pressure and extreme temperatures.
- Strength: The materials used in these castings ensure they can endure high stress without deforming.
- Precision: The casting process allows for high-precision parts that fit seamlessly into complex valve systems.
These features make high pressure valve castings invaluable for critical infrastructure.
Common Mistakes with High Pressure Valve Castings
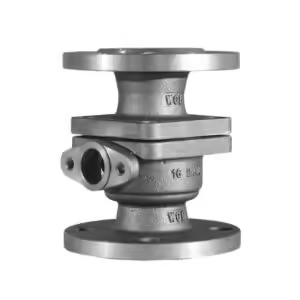
1. Choosing the Wrong Material
One of the most frequent mistakes when dealing with high-pressure components such as valve castings is the incorrect selection of materials. The material chosen for any valve casting is vital as it determines how well the casting can withstand extreme pressures and environmental factors. If the material is too weak or not suited for high-pressure environments, it can fail unexpectedly, which could lead to major system malfunctions and catastrophic results.
How to Avoid This Mistake
To avoid choosing the wrong material for your valve casting, it’s crucial to thoroughly understand the specific demands of the application. Factors such as the pressure levels, temperature ranges, and the types of fluids or gases being handled must all be considered. Working closely with manufacturers and material experts will ensure that the chosen material is appropriate for the operating conditions. This step is vital to maintaining the safety and longevity of the valve system.
2. Ignoring Casting Defects
Another common problem is overlooking defects during the manufacturing process of the valve castings. Defects like air pockets, cracks, or porosity within the casting material can severely affect the integrity of the final product. These issues can lead to leaking valves, compromised strength, and, in worst-case scenarios, catastrophic failures in the system.
How to Avoid This Mistake
To prevent these issues, it is essential to inspect each casting thoroughly before installation. Ensure that quality control processes are in place, including non-destructive testing techniques such as ultrasonic testing or X-ray inspections. These methods will help identify any defects early, allowing them to be corrected before the components are put into service. Additionally, it’s important to source your castings from reputable manufacturers who follow strict quality assurance protocols to ensure each part meets high standards.
3. Improperly Handling High Pressure Valve Castings
Handling valve castings improperly during their transport or installation is a significant source of damage. Since these castings are often quite heavy and fragile, mishandling can lead to cracks or deformations. Improper handling can result in costly repairs, system downtime, and even safety risks.
How to Avoid This Mistake
To prevent damage, ensure that the castings are moved using the correct equipment and that all personnel involved in the process are adequately trained in handling heavy and delicate components. Always follow the manufacturer’s recommendations for lifting and positioning the parts to prevent unnecessary stress on the material. Protective packaging, padding, and the use of cranes or lifting devices can minimize the risk of physical damage during transportation and installation.
4. Failing to Consider Long-Term Maintenance
An often-overlooked aspect in the use of valve castings is the failure to properly plan for long-term maintenance. Over time, these components are subjected to constant wear and tear, extreme pressure, and potential exposure to corrosive substances. Neglecting regular maintenance can lead to system failures, leaks, and potential safety hazards that could have been avoided.
How to Avoid This Mistake
Establishing a comprehensive maintenance plan is key to ensuring the longevity and performance of your valve components. Regular inspections should be carried out to check for signs of wear, corrosion, or fatigue. Cleaning and lubrication schedules should be strictly followed, and valves should be replaced or repaired as necessary. Consider investing in materials that are specifically designed to resist corrosion, high temperatures, and mechanical wear, as this will help extend the lifespan of the valves and reduce the frequency of maintenance.
5. Not Considering the Impact of Pressure Variations
One of the most significant mistakes in using valve castings is the failure to account for pressure variations in the system. Many industrial systems experience fluctuations in pressure during operation, which can put additional stress on the components. If the valve castings aren’t designed to handle such pressure changes, premature failure is inevitable, leading to potential system failures or even dangerous accidents.
How to Avoid This Mistake
To prevent this issue, work closely with engineers and casting manufacturers who can design components that are specifically tailored to handle fluctuating pressures. These components should be able to withstand varying operating conditions, whether the pressure is consistently high or subject to fluctuations. Proper design will ensure that the valve castings perform optimally even under pressure surges, helping to avoid premature wear and failures.
Best Practices
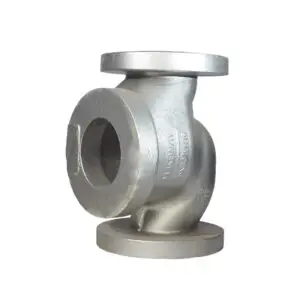
While avoiding mistakes is critical, implementing best practices for high pressure valve castings can also help improve performance and reliability. Some best practices include:
- Select the Right Manufacturing Process: The casting process should be chosen based on the application. Precision casting, for instance, can improve the accuracy and strength of the final product.
- Invest in High-Quality Materials: The materials used in high pressure valve castings should be carefully selected to ensure durability and resistance to corrosion and high temperatures.
- Ensure Proper Testing: Before installation, conduct rigorous tests such as pressure testing and non-destructive testing to ensure the castings are safe for use.
Table: Comparison of Materials for High Pressure Valve Castings
Material Type | Strength | Temperature Resistance | Korrosionsbeständigkeit | Cost |
---|---|---|---|---|
Edelstahl | Hoch | Exzellent | Gut | Hoch |
Kohlenstoffstahl | Medium | Gut | Fair | Mäßig |
Legierter Stahl | Hoch | Exzellent | Exzellent | Hoch |
Ductile Iron | Medium | Fair | Gut | Niedrig |
This table compares different materials commonly used for high pressure valve castings. The material selected will depend on the specific needs of the application, balancing cost against performance factors like strength and corrosion resistance.
Abschluss
High pressure valve castings are a critical component in many industrial applications, and avoiding common mistakes can help ensure their long-term performance and reliability. By selecting the right material, properly handling and maintaining the castings, and addressing common issues such as defects and pressure fluctuations, you can improve the efficiency and safety of your systems. Always consult with experts to make informed decisions about your high pressure valve castings and ensure that your equipment operates smoothly.
Häufig gestellte Fragen
What are high pressure valve castings used for?
High pressure valve castings are primarily used in industries that require valves capable of withstanding extreme pressure, such as oil and gas, chemical processing, and power generation.
How do I choose the right material for high pressure valve castings?
The right material depends on the specific pressure, temperature, and environmental conditions the valve will be exposed to. Consult with engineers and manufacturers to select the best material for your needs.
What are some common defects in high pressure valve castings?
Common defects include cracks, air pockets, and porosity. These defects can compromise the valve’s performance and safety, so they should be thoroughly inspected before use.
How can I prevent corrosion in high pressure valve castings?
Choosing corrosion-resistant materials and implementing regular maintenance practices, such as cleaning and coating, can help prevent corrosion and extend the lifespan of high pressure valve castings.
Produktkategorien
- Ventilteile
- Wasserpumpenteile
- Lagergehäuseteile
- Druckgussteile
- Pumpenprodukte aus Edelstahl
- Pumpenprodukte aus Gusseisen
- Ventilteile für den Automobilgebrauch
- Autoteile
- Ventilteile für den zivilen Gebrauch
- Vakuumpumpenteile KF
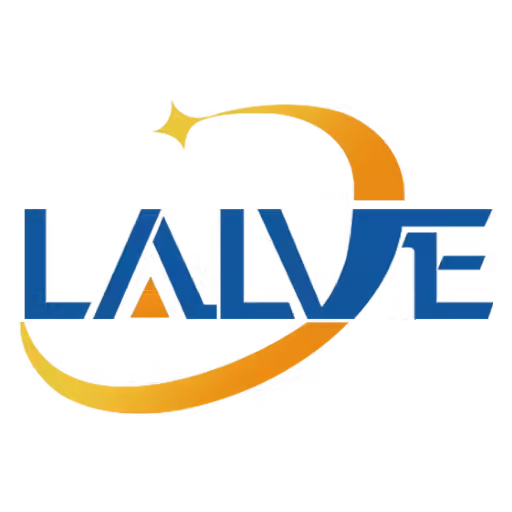