How to Extend the Lifespan of Pump Valve Castings: 5 Tips
¡Bienvenido a mi blog!
Antes de profundizar en el contenido, me encantaría que me acompañaras en mis redes sociales, donde comparto más información, interactúo con la comunidad y publico actualizaciones. Puedes conectar conmigo de la siguiente manera:
Facebook:https://www.facebook.com/people/Shanghai-Leierwo-Industry-Trade-Co-Ltd/61574022590718/
Ahora, comencemos nuestro viaje juntos. Espero que el contenido aquí les resulte interesante, interesante y valioso.
Tabla de contenido
Introducción
Pump valve castings are essential components in industries such as oil and gas, water treatment, and manufacturing. These castings ensure the efficient operation of pumps and valves, which are critical for controlling fluid flow and maintaining system integrity. However, pump valve castings are often exposed to harsh conditions, including high pressure, corrosive fluids, and extreme temperatures, which can lead to wear, corrosion, and eventual failure.
Extending the lifespan of pump valve castings is not only cost-effective but also crucial for minimizing downtime and maintaining operational efficiency. In this comprehensive guide, we’ll explore how to extend the lifespan of pump valve castings with 5 expert tips. We’ll also address common challenges, best practices, and frequently asked questions to provide a complete understanding of this critical topic.
Understanding Pump Valve Castings
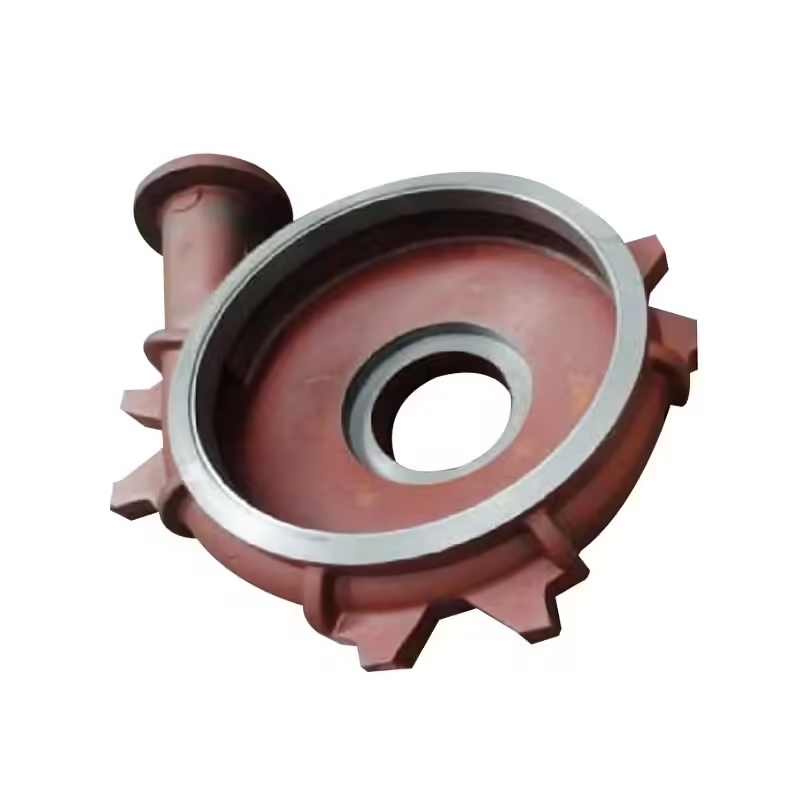
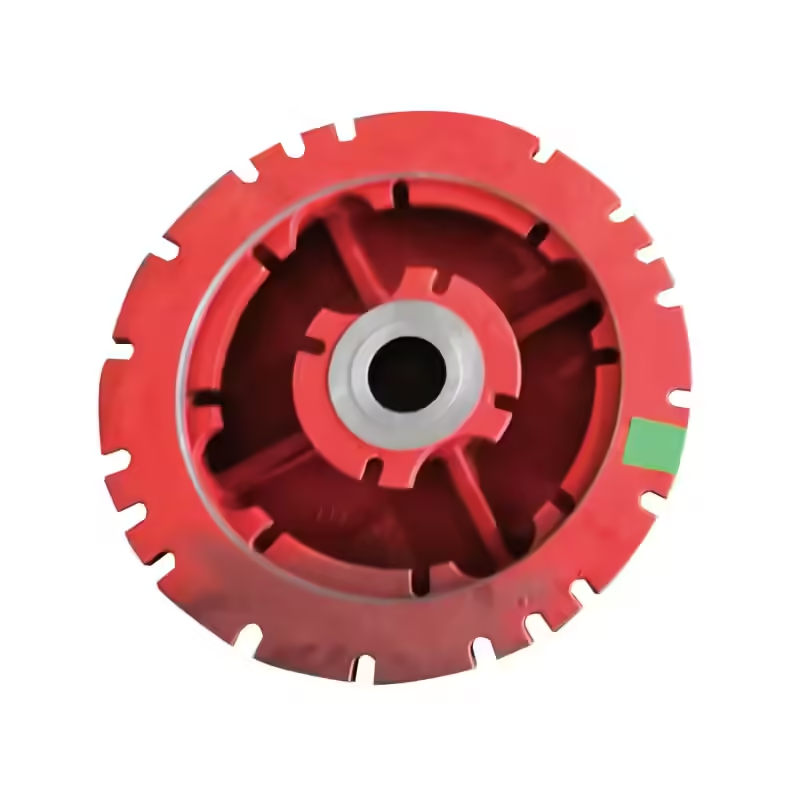
What Are Pump Valve Castings?
Pump valve castings are metal components manufactured through casting processes such as sand casting, investment casting, or die casting. They are typically made from materials like stainless steel, ductile iron, brass, or bronze, chosen for their strength, durability, and resistance to corrosion.
These castings form the structural framework of pumps and valves, ensuring they can withstand the rigors of industrial applications. They are used in a wide range of industries, including:
- Oil and gas
- Water and wastewater treatment
- Chemical processing
- Power generation
- Manufacturing
Why Is Lifespan Extension Important?
Pump valve castings are subject to significant stress and wear over time. Premature failure can lead to costly repairs, unplanned downtime, and even safety hazards. By implementing strategies to extend their lifespan, businesses can:
- Reduce maintenance and replacement costs
- Improve operational efficiency
- Enhance safety and reliability
- Minimize environmental impact
5 Expert Tips to Extend the Lifespan
Tip 1: Regular Inspection and Maintenance
Regular inspections are the cornerstone of extending the lifespan of pump valve castings. Inspections help identify early signs of wear, corrosion, or damage, allowing for timely interventions.
Key Inspection Practices:
- Visual Checks: Look for cracks, pitting, or erosion on the casting surface.
- Non-Destructive Testing (NDT): Use techniques like ultrasonic testing or magnetic particle inspection to detect internal flaws.
- Leak Detection: Check for leaks around the castings, which may indicate seal failure or cracks.
A well-documented maintenance schedule ensures that inspections are conducted consistently and that any issues are addressed promptly.
Tip 2: Proper Installation Techniques
Improper installation is a common cause of premature failure in pump valve castings. Misalignment, over-tightening, or using incorrect tools can introduce stress points that lead to cracks or deformation.
Best Practices for Installation:
- Follow the manufacturer’s guidelines for installation procedures.
- Use calibrated tools to ensure proper torque application.
- Verify alignment during installation to prevent stress on the castings.
Tip 3: Use Corrosion-Resistant Materials
Corrosion is one of the most significant threats to pump valve castings, particularly in industries dealing with corrosive fluids or environments. Choosing the right materials and coatings can significantly enhance corrosion resistance.
Material Options:
- Stainless Steel: Offers excellent resistance to corrosion and high temperatures.
- Ductile Iron: Provides strength and durability, often used in water and wastewater applications.
- Bronze or Brass: Ideal for marine environments due to their resistance to saltwater corrosion.
Protective Coatings:
- Epoxy Coatings: Provide a barrier against corrosive chemicals.
- Zinc Coatings: Offer galvanic protection for iron castings.
- Ceramic Coatings: Enhance resistance to abrasion and corrosion.
Tip 4: Monitor Operating Conditions
Pump valve castings are designed to operate within specific pressure, temperature, and fluid velocity ranges. Exceeding these limits can accelerate wear and lead to failure.
Monitoring Strategies:
- Install sensors to track pressure and temperature in real time.
- Regularly check fluid properties, such as pH and viscosity, to ensure they are within acceptable ranges.
- Use flow meters to monitor fluid velocity and prevent cavitation, which can damage castings.
Tip 5: Implement a Cleaning Routine
Debris, sediment, and contaminants can accumulate on pump valve castings, leading to blockages, corrosion, or abrasion. A regular cleaning routine helps maintain optimal performance and extends the lifespan of the castings.
Cleaning Methods:
- Mechanical Cleaning: Use brushes or scrapers to remove buildup.
- Chemical Cleaning: Apply cleaning agents to dissolve contaminants.
- Ultrasonic Cleaning: Use high-frequency sound waves to remove debris from hard-to-reach areas.
Common Challenges with Pump Valve Castings
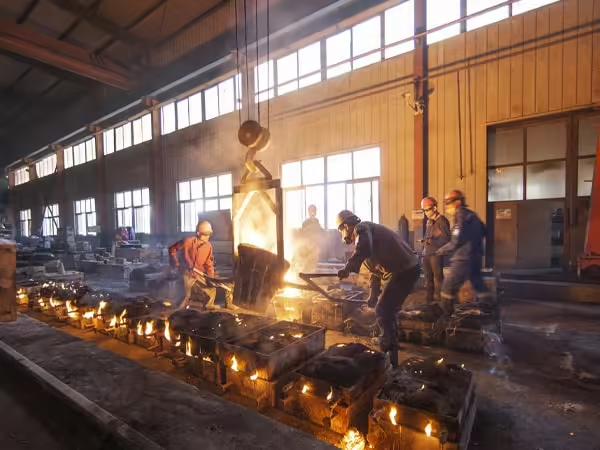
Challenge 1: Wear and Tear
Pump valve castings are subject to mechanical wear due to friction, abrasive fluids, or high-velocity flow. Over time, this can lead to thinning of the casting walls or surface degradation.
Solutions:
- Use wear-resistant materials like hardened steel or ceramic coatings.
- Implement regular inspections to detect wear early.
- Optimize fluid flow to reduce abrasion.
Challenge 2: Corrosion
Corrosion occurs when the casting material reacts with its environment, leading to material loss and structural weakness. This is particularly problematic in industries dealing with chemicals or saltwater.
Solutions:
- Choose corrosion-resistant materials like stainless steel or bronze.
- Apply protective coatings to create a barrier against corrosive agents.
- Regularly clean castings to remove corrosive deposits.
Challenge 3: Improper Handling
Improper handling during installation, maintenance, or transportation can cause physical damage to pump valve castings, such as cracks or dents.
Solutions:
- Train staff on proper handling techniques.
- Use lifting equipment and protective padding during transportation.
- Follow manufacturer guidelines for installation and maintenance.
Best Practices for Pump Valve Castings Maintenance
Practice | Descripción |
---|---|
Regular Inspections | Check for cracks, corrosion, or wear periodically. |
Proper Cleaning | Remove debris and contaminants to prevent blockages. |
Material Selection | Use corrosion-resistant materials for harsh environments. |
Monitoring Conditions | Ensure pressure, temperature, and fluid velocity remain within safe limits. |
Professional Installation | Follow manufacturer guidelines to avoid misalignment or stress. |
Conclusión
Extending the lifespan of pump valve castings is essential for maintaining operational efficiency, reducing costs, and ensuring safety in industrial applications. By following the 5 expert tips outlined in this guide—regular inspection and maintenance, proper installation, using corrosion-resistant materials, monitoring operating conditions, and implementing a cleaning routine—you can significantly enhance the durability and performance of your castings.
Additionally, understanding common challenges and adopting best practices will help you address potential issues before they escalate. Whether you’re an engineer, technician, or industry professional, this comprehensive approach will empower you to maximize the lifespan of your pump valve castings and optimize your operations.
PREGUNTAS FRECUENTES
What materials are best ?
A: The choice of material depends on the application. Stainless steel, ductile iron, and bronze are popular options due to their strength, durability, and resistance to corrosion.
How often should I inspect pump valve castings?
A: The frequency of inspections depends on the operating conditions. For most industries, inspections every 3-6 months are recommended.
Can I repair damaged pump valve castings?
A: Minor damage can often be repaired using welding or epoxy fillers. However, severely damaged castings should be replaced to ensure safety and efficiency.
What causes corrosion in pump valve castings?
A: Corrosion is typically caused by exposure to corrosive chemicals, saline environments, or high humidity. Using corrosion-resistant materials and coatings can mitigate this issue.
How can I prevent wear and tear on castings?
A: Regular maintenance, proper installation, and monitoring operating conditions are key to preventing excessive wear. Additionally, using wear-resistant materials can help.
What are the signs of pump valve casting failure?
A: Common signs include visible cracks, leaks, reduced performance, and unusual noises. Regular inspections can help detect these issues early.
Can coatings extend the lifespan of pump valve castings?
A: Yes, protective coatings like epoxy, zinc, or ceramic can enhance resistance to corrosion, abrasion, and wear, significantly extending the lifespan of castings.
How do I choose the right pump valve castings for my application?
A: Consider factors such as the type of fluid, operating pressure and temperature, and environmental conditions. Consulting with a manufacturer or expert can also help.
What is cavitation, and how does it affect pump valve castings?
A: Cavitation occurs when vapor bubbles form and collapse in a liquid, creating shockwaves that can damage castings. Monitoring fluid velocity and pressure can help prevent cavitation.
Are there industry standards for pump valve castings?
A: Yes, standards like ASTM, ISO, and API provide guidelines for the design, manufacturing, and testing of pump valve castings to ensure quality and reliability.
Categorías de productos
- Piezas de válvulas
- Piezas de la bomba de agua
- Piezas de la caja de cojinetes
- Piezas de fundición a presión
- Productos para bombas de acero inoxidable
- Productos para bombas de hierro fundido
- Piezas de válvulas para automóviles
- Recambios para automóviles
- Piezas de válvulas para uso civil
- Piezas de bomba de vacío KF
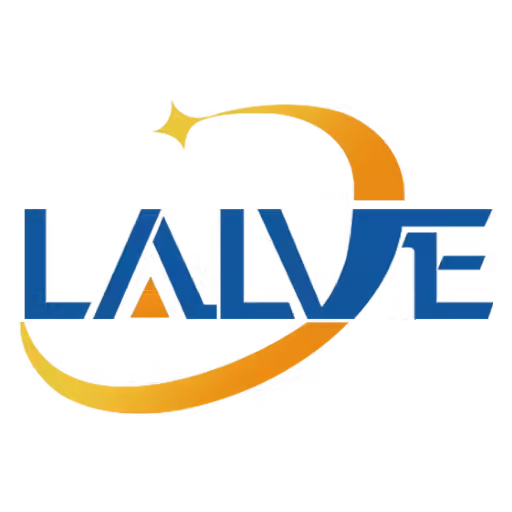