Water Pump Castings: How to Accurately Detect Their Defects
¡Bienvenido a mi blog!
Antes de profundizar en el contenido, me encantaría que me acompañaras en mis redes sociales, donde comparto más información, interactúo con la comunidad y publico actualizaciones. Puedes conectar conmigo de la siguiente manera:
Facebook:https://www.facebook.com/people/Shanghai-Leierwo-Industry-Trade-Co-Ltd/61574022590718/
Ahora, comencemos nuestro viaje juntos. Espero que el contenido aquí les resulte interesante, interesante y valioso.
Tabla de contenido
Introducción
Water pump casting is a critical component in various industrial and mechanical systems. Its quality directly impacts the performance, efficiency, and longevity of the equipment it serves. However, not all water pump castings are created equal. Poor quality casting can lead to frequent breakdowns, increased maintenance costs, and even safety hazards. In this blog, we’ll explore how to quickly identify subpar water pump casting, ensuring you make informed decisions and avoid costly mistakes.
What is Water Pump Casting?

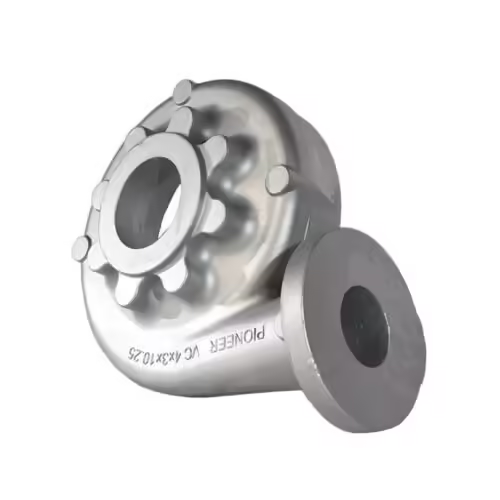
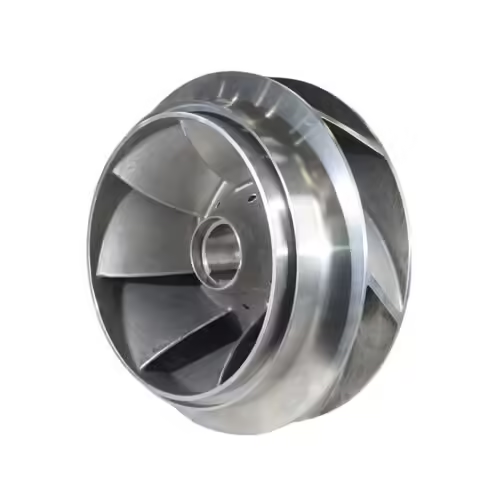
Water pump casting refers to the process of creating pump components by pouring molten metal into molds. These components are essential for the proper functioning of water pumps, which are widely used in industries like agriculture, automotive, and manufacturing. The casting process involves several steps, including mold preparation, metal melting, pouring, and finishing. The quality of the final product depends on factors such as material selection, casting technique, and post-processing.
Key Indicators of Poor Quality Water Pump Casting
When evaluating the quality of cast components, particularly those used in fluid systems, certain red flags can indicate subpar manufacturing. Here’s an expanded look at the key indicators that may suggest inferior quality in these essential parts.
1. Surface Imperfections
One of the most obvious signs of poor craftsmanship in cast components is the presence of surface defects. These can include cracks, pores, uneven textures, or visible blemishes. Such imperfections not only detract from the appearance but also compromise the structural integrity of the part. Over time, these flaws can lead to premature failure, especially under high-stress conditions.
To avoid such issues, always conduct a thorough visual inspection before making a purchase. Using tools like magnifying glasses or microscopes can help identify smaller defects that might otherwise go unnoticed.
2. Dimensional Inaccuracies
Precision is paramount when it comes to manufacturing parts for mechanical systems. Components that deviate from the required dimensions can cause misalignment, improper fitting, or even complete system failure. For instance, a slightly oversized or undersized part may not fit correctly, leading to leaks or reduced efficiency.
To ensure accuracy, use precise measuring tools such as calipers or micrometers to compare the part’s dimensions against the technical specifications. Even minor discrepancies can have significant consequences, so attention to detail is critical.
3. Weak Material Strength
The durability and performance of cast parts depend heavily on the quality of the materials used. Inferior materials or improper alloy compositions can result in components that are unable to withstand high pressure, wear, or corrosive environments. This can lead to frequent breakdowns and increased maintenance costs.
To verify material quality, conduct tests such as hardness testing, tensile strength analysis, or chemical composition checks. These tests can confirm whether the material meets the necessary industry standards.
4. Poor Finishing and Coating
A well-manufactured part should have a smooth, even finish and a proper coating to protect against corrosion and wear. Rough edges, incomplete coatings, or inconsistencies in finishing are clear indicators of poor quality. Such defects can accelerate wear and tear, reducing the lifespan of the component.
During inspection, pay close attention to the surface finish and coating quality. A high-quality product should feel smooth to the touch and exhibit no signs of flaking or uneven application.
5. Internal Defects
Not all defects are visible on the surface. Internal issues such as voids, inclusions, or improper grain structure can significantly compromise the integrity of the part. These hidden flaws can lead to unexpected failures, even if the component appears to be in good condition externally.
To detect internal defects, employ non-destructive testing (NDT) methods like ultrasonic testing, X-ray inspection, or magnetic particle testing. These techniques allow you to examine the internal structure without damaging the part.
Summary of Key Indicators
To quickly identify subpar quality in cast components, focus on the following aspects:
- Surface Quality: Look for cracks, pores, or uneven textures.
- Dimensional Accuracy: Ensure the part meets the required specifications.
- Material Strength: Verify the material’s durability through testing.
- Finishing and Coating: Check for smoothness and proper application.
- Internal Integrity: Use NDT methods to detect hidden flaws.
By understanding these indicators and implementing rigorous inspection processes, you can avoid the pitfalls of poor-quality components and ensure the reliability of your systems.
Common Causes of Poor Quality Water Pump Casting
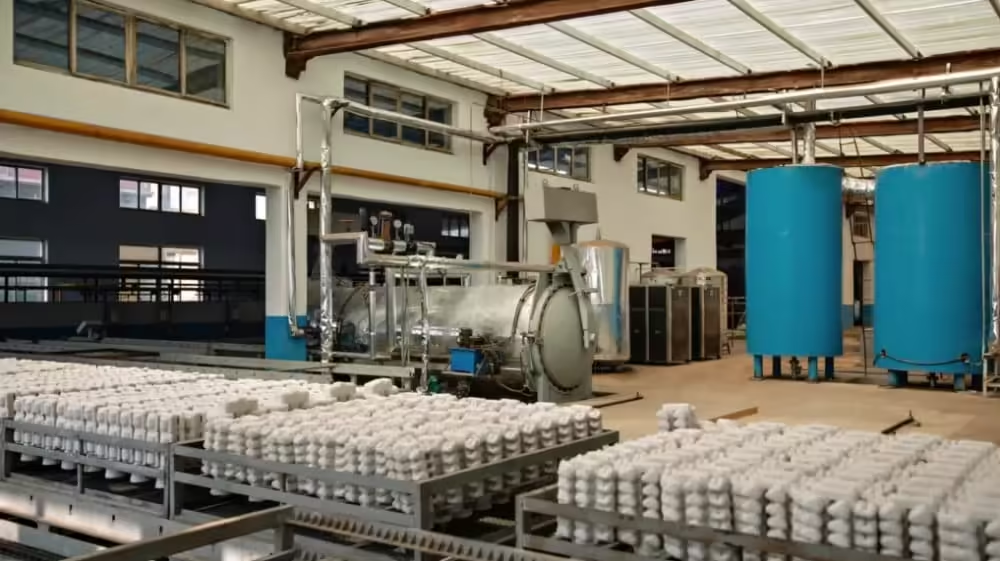
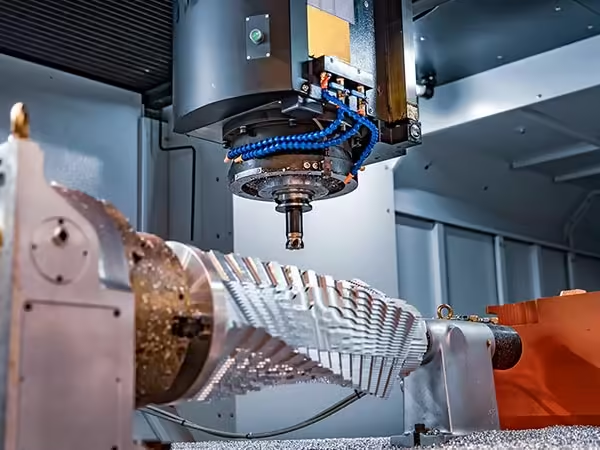
Inadequate Mold Design
The mold used in the casting process plays a significant role in determining the quality of the final product. Poorly designed molds can lead to defects like air pockets, incomplete filling, or uneven cooling.
Improper Cooling Process
Rapid or uneven cooling can cause internal stresses and cracks in the casting. A controlled cooling process is essential to ensure the structural integrity of the component.
Low-Quality Raw Materials
Using substandard or contaminated raw materials can result in weak and unreliable water pump castings. Always verify the quality and source of the materials used in the casting process.
How to Test Water Pump Casting Quality
Visual Inspection
Start by examining the casting for any visible defects, such as cracks, pores, or rough surfaces. A magnifying glass or microscope can help identify smaller imperfections.
Dimensional Measurement
Use calipers, micrometers, or other measuring tools to check the dimensions of the casting. Compare the measurements with the technical specifications to ensure accuracy.
Material Testing
Conduct tests to determine the material properties of the casting, such as hardness, tensile strength, and chemical composition. These tests can reveal whether the material meets the required standards.
Non-Destructive Testing (NDT)
NDT methods like ultrasonic testing, X-ray inspection, and magnetic particle testing can detect internal defects without damaging the casting. These techniques are particularly useful for identifying hidden issues.
Table: Comparison of High-Quality vs. Poor Quality Water Pump Casting
Aspect | High-Quality Casting | Poor Quality Casting |
---|---|---|
Surface Finish | Smooth and even | Rough or porous |
Dimensional Accuracy | Precise and consistent | Inaccurate or inconsistent |
Material Strength | High strength and durability | Weak and prone to failure |
Internal Structure | Uniform and defect-free | Voids, inclusions, or cracks |
Coating and Finishing | Complete and corrosion-resistant | Incomplete or inconsistent |
Steps to Avoid Poor Quality Water Pump Casting
Ensuring the quality of water pump castings is critical for the performance and longevity of the pumps. Poor quality castings can lead to frequent failures, increased maintenance costs, and operational inefficiencies. Here are detailed steps to help you avoid poor quality water pump castings:
Choose Reputable Suppliers
Work with suppliers who have a proven track record of delivering high-quality water pump castings. Check their certifications, customer reviews, and industry reputation.
Verify Material Specifications
Ensure the casting materials meet the required standards and specifications. Request material test reports from the supplier to confirm the quality.
Implement Quality Control Measures
Incoming Inspection: Conduct thorough inspections of raw materials and components upon receipt. This includes verifying dimensions, surface finish, and material properties.
In-Process Inspection: Implement quality checks at various stages of production, such as during molding, pouring, and cooling. This helps in identifying and rectifying defects early in the process.
Final Inspection: Perform comprehensive inspections on finished castings, including visual inspections, dimensional checks, and non-destructive testing (NDT) methods like ultrasonic testing, radiography, or dye penetrant testing.
Testing and Validation: Conduct performance tests to ensure the castings meet the required operational standards. This may include pressure testing, leak testing, and endurance testing.
Invest in Training
Train your team to identify potential issues and conduct thorough inspections. Knowledgeable staff can help prevent poor quality castings from entering your supply chain.
Conclusión
Identifying poor quality water pump casting quickly is essential to ensure the reliability and efficiency of your equipment. By understanding the key indicators of subpar casting, implementing rigorous testing methods, and working with reputable suppliers, you can avoid costly mistakes and maintain optimal system performance. Always prioritize quality and invest in thorough inspections to safeguard your operations.
PREGUNTAS FRECUENTES
What are the most common defects in water pump casting?
Common defects include surface cracks, porosity, dimensional inaccuracies, and internal voids.
How can I test the material strength of a water pump casting?
Material strength can be tested using methods like hardness testing, tensile testing, and chemical composition analysis.
What are the consequences of using poor quality water pump casting?
Poor quality castings can lead to equipment failure, increased maintenance costs, and safety risks.
Can internal defects in water pump casting be repaired?
In most cases, internal defects cannot be repaired and may require the casting to be replaced.
How do I choose a reliable supplier for water pump casting?
Look for suppliers with industry certifications, positive customer reviews, and a history of delivering high-quality products.
Categorías de productos
- Piezas de válvulas
- Piezas de la bomba de agua
- Piezas de la caja de cojinetes
- Piezas de fundición a presión
- Productos para bombas de acero inoxidable
- Productos para bombas de hierro fundido
- Piezas de válvulas para automóviles
- Recambios para automóviles
- Piezas de válvulas para uso civil
- Piezas de bomba de vacío KF
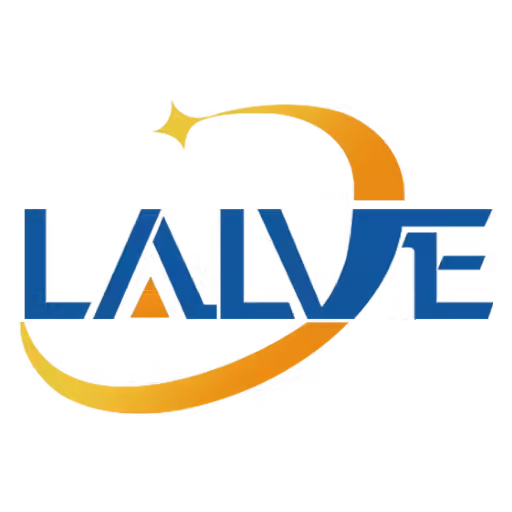