4 Costly Gate Valve Castings Myths
Selamat Datang ke Blog Saya!
I’m thrilled to have you here! Before we dive into the content, I’d love for you to join me on my social media platforms. It’s where I share extra insights, connect with our amazing community, and keep you updated on the latest news. Here’s how you can stay connected:
📘 Facebook: Shanghai Leierwo Industry Trade Co., Ltd.
Now, let’s embark on this journey together! I hope you find the content here not only insightful but also inspiring and valuable. Let’s get started!
Jadual Kandungan
pengenalan
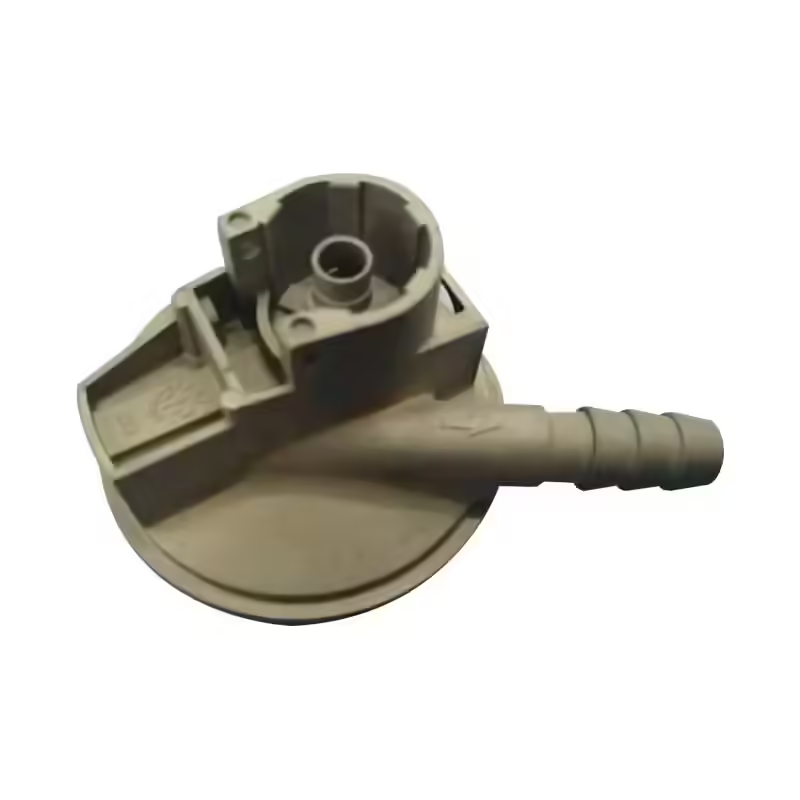
In industrial piping systems, gate valve castings play a critical role in controlling fluid flow. They’re used in water systems, oil and gas pipelines, power plants, and countless other heavy-duty applications. However, despite their widespread use and significance, many professionals and buyers still fall victim to a number of misconceptions surrounding gate valve castings.
These misunderstandings often lead to poor decision-making, increased operational costs, and compromised safety. This article aims to bust the four most costly myths associated with gate valve castings while educating readers on what truly matters when choosing or working with them.
By gaining clarity on these myths, you’ll be better positioned to choose the right materials, suppliers, and processes that enhance durability and efficiency in your systems.
Let’s take a closer look at each myth and reveal what the industry experts already know but few discuss openly.
Myth 1: All Gate Valve Castings Are the Same
One of the most common and damaging myths circulating in the industrial valve world is that all gate valve castings are created equal. This myth persists because the differences between high-quality and subpar castings are not always visible to the naked eye. On the surface, many castings may appear identical—especially when viewed as standardized components lined up in a warehouse. However, beneath this visual similarity lies a spectrum of variation in material integrity, casting precision, and long-term durability.
Why It Matters
The assumption that all gate valve castings are equivalent can lead to procurement decisions that compromise the performance of entire systems. In practice, the casting quality can significantly influence:
- The ability of the valve to withstand pressure and temperature extremes.
- The likelihood of internal corrosion or cracking due to impurities.
- The valve’s overall dimensional stability under long-term use.
Substandard castings are often the result of poorly controlled foundry environments. These may include the use of recycled or non-certified metals, shortcuts in mold preparation, or hasty cooling processes that result in uneven density. These factors can introduce tiny cracks, shrinkage cavities, or inconsistent wall thicknesses that don’t become apparent until the valve is under stress.
Once installed, these weak points often reveal themselves as operational failures—leaks, ruptures, or misalignment of critical sealing surfaces. In sensitive industries such as oil refining or water treatment, these failures can not only lead to costly shutdowns but also pose significant safety hazards.
What to Look For Instead
- Check for compliance with international standards (e.g., ASTM, ASME, ISO).
- Request detailed material certifications and inspection reports.
- Work with suppliers who use high-integrity casting methods like investment casting or shell molding when appropriate.
Understanding that not all gate valve castings are the same can save you time and money in both the short and long term.
Myth 2: Gate Valve Castings Don’t Affect Flow Efficiency
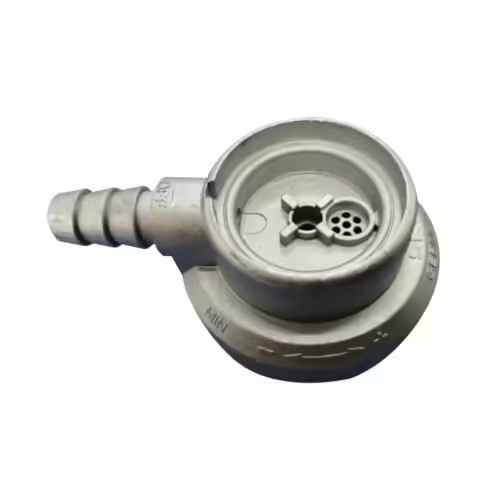
Another widespread myth is the belief that the casting quality of a gate valve has little to no influence on its ability to control fluid flow. Many engineers and buyers place emphasis on the valve’s external dimensions or pressure ratings but overlook the critical role that casting quality plays in flow dynamics. While the valve design itself certainly affects efficiency, it’s a mistake to think that the casting is merely a passive shell.
Internal Finish and Flow Dynamics
Rough or uneven interior surfaces caused by poor casting methods can lead to turbulence in the fluid flow. This increases pressure drop across the valve, reduces overall efficiency, and may even cause cavitation in high-pressure systems.
Poor alignment of the internal gate and seating surfaces can also prevent proper sealing, leading to leaks or flow disruptions.
The Cost of Overlooking This
Failing to consider the impact of casting quality can lead to both direct and indirect costs. Some of these include:
- Energy inefficiency: Poor flow characteristics force pumps to work harder, increasing operational energy use and carbon footprint.
- Frequent maintenance: System operators may need to repeatedly reseat, repair, or replace valves that should have lasted significantly longer.
- Downtime and lost production: In industrial environments, even a few hours of unplanned downtime can translate into tens of thousands of dollars in lost output.
In a real-world case study, a water treatment facility replaced 50 gate valves sourced from a low-cost overseas supplier. Within 18 months, over 70% of those valves required either repair or full replacement due to internal erosion and sealing issues. After switching to a manufacturer offering precision-cast and fully machined valve bodies, the maintenance schedule improved dramatically, and the total cost of ownership was significantly reduced over the next 5 years.
Gate Valve Casting Methods and Their Impact
To better understand how casting methods influence the final product, here’s a comparison of some of the most commonly used techniques:
Casting Method | Surface Finish Quality | Cost Efficiency | Ideal For | Drawbacks |
---|---|---|---|---|
Sand Casting | Sederhana | tinggi | Large valve bodies | Less dimensional accuracy |
Investment Casting | Cemerlang | Sederhana | Intricate parts and tight tolerances | Higher material costs |
Shell Molding | bagus | Sederhana | Medium-sized parts with smooth finish | Requires specialized equipment |
Centrifugal Casting | tinggi | Low for large runs | Round and symmetrical components | Limited shape complexity |
Die Casting | Cemerlang | Low for high volume | Small components, high-volume runs | Expensive tooling for small batches |
This table highlights how your choice of casting method directly affects cost, durability, and functionality.
Myth 3: Gate Valve Castings Never Need Post-Processing
It’s a mistake to believe that once gate valve castings are produced, they are immediately ready for installation. While some basic castings may seem ready, most high-performance components require additional finishing steps.
Importance of Machining and Heat Treatment
After casting, parts often undergo machining to achieve precise tolerances and smoother sealing surfaces. Heat treatment is also essential in many cases to improve mechanical properties, such as hardness and tensile strength.
Skipping these post-processing steps can lead to:
- Poor valve sealing.
- Premature failure under stress.
- Incompatibility with high-temperature or high-pressure systems.
Some manufacturers offer full in-house post-processing, ensuring that each gate valve casting is optimized for performance before delivery. Always check what level of finishing is included in the casting service you purchase.
Myth 4: Cheaper Gate Valve Castings Offer Better ROI
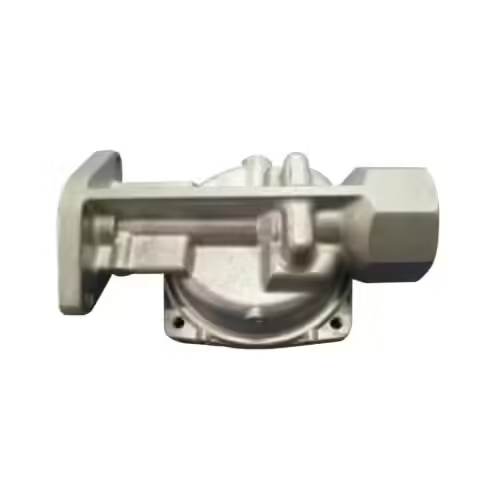
This myth is particularly dangerous because it appeals to the desire for short-term savings. Many buyers assume that lower-priced gate valve castings equate to better ROI, especially when purchasing in bulk.
The Hidden Costs of Low-Quality Castings
In reality, cheaper castings often lead to frequent breakdowns, unplanned downtime, and expensive repairs. Low-grade materials may not hold up under thermal or mechanical stress, leading to cracking, deformation, or corrosion.
Additionally, low-cost castings usually come from sources that do not perform rigorous testing or quality checks, leaving you vulnerable to failures that can halt entire operations.
Long-Term Value Over Upfront Savings
Spending more on high-quality gate valve castings from reputable sources typically results in:
- Fewer maintenance needs.
- Longer service life.
- Higher safety and compliance with industry standards.
Investing in quality from the start is not just a cost—it’s a risk management strategy.
Kesimpulan
Busting these four costly myths around gate valve castings shows how important it is to prioritize quality, precision, and the right production methods. Whether you’re in procurement, engineering, or operations, your understanding of how gate valve castings influence performance can make a major difference in system reliability and cost-effectiveness.
Rather than chasing the lowest price, focus on casting quality, post-processing procedures, and compliance with recognized standards. It’s not just about buying a valve component—it’s about securing the integrity of your entire system.
Soalan Lazim
What materials are typically used in gate valve castings?
Most gate valve castings are made from ductile iron, stainless steel, carbon steel, bronze, or special alloys depending on the application’s temperature and pressure requirements.
How do I know if a gate valve casting meets international standards?
Look for certifications such as ISO 9001, ASTM A216, A351, or ASME compliance. Also request documentation like Mill Test Reports (MTRs) from the supplier.
Can I use sand castings for high-pressure applications?
While sand castings are cost-effective, they may not always meet the precision or strength required for high-pressure systems. In such cases, investment or centrifugal casting may be more appropriate.
How long do gate valve castings typically last?
The service life depends on factors such as material quality, casting method, operational conditions, and maintenance frequency. High-quality castings can last several decades under normal use.
Is it possible to custom-order gate valve castings?
Yes, many manufacturers offer custom casting services tailored to specific size, material, and pressure needs. Always verify the manufacturer’s capabilities and quality control processes before placing custom orders.
Kategori Produk
- Bahagian Injap
- Bahagian Pam Air
- Bahagian Kotak Galas
- Bahagian Die Casting
- Produk Pam Keluli Tahan Karat
- Produk Pam Besi Tuang
- Bahagian Injap Untuk Kegunaan Kereta
- Bahagian Kenderaan
- Bahagian Injap Untuk Kegunaan Awam
- Bahagian Pam Vakum KF
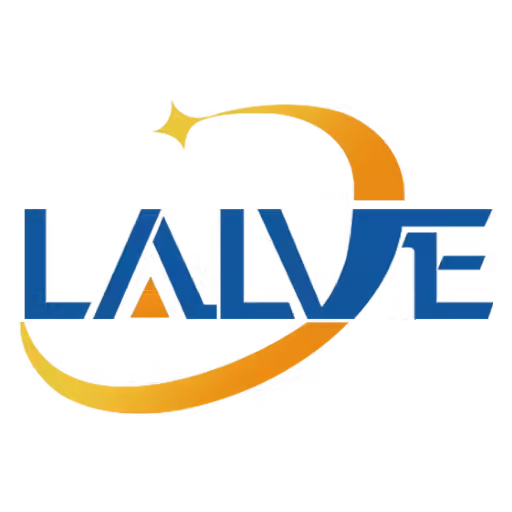