6 Key Features of High-Performance Casting Impeller
Selamat Datang ke Blog Saya!
Sebelum kita menyelami kandungannya, saya ingin anda menyertai saya di platform media sosial saya di mana saya berkongsi lebih banyak cerapan, melibatkan diri dengan komuniti dan menyiarkan kemas kini. Begini cara anda boleh berhubung dengan saya:
Facebook:https://www.facebook.com/people/Shanghai-Leierwo-Industry-Trade-Co-Ltd/61574022590718/
Sekarang, mari kita mulakan perjalanan kita bersama-sama. Saya harap anda mendapati kandungan di sini berwawasan, menarik dan berharga.
Jadual Kandungan
pengenalan
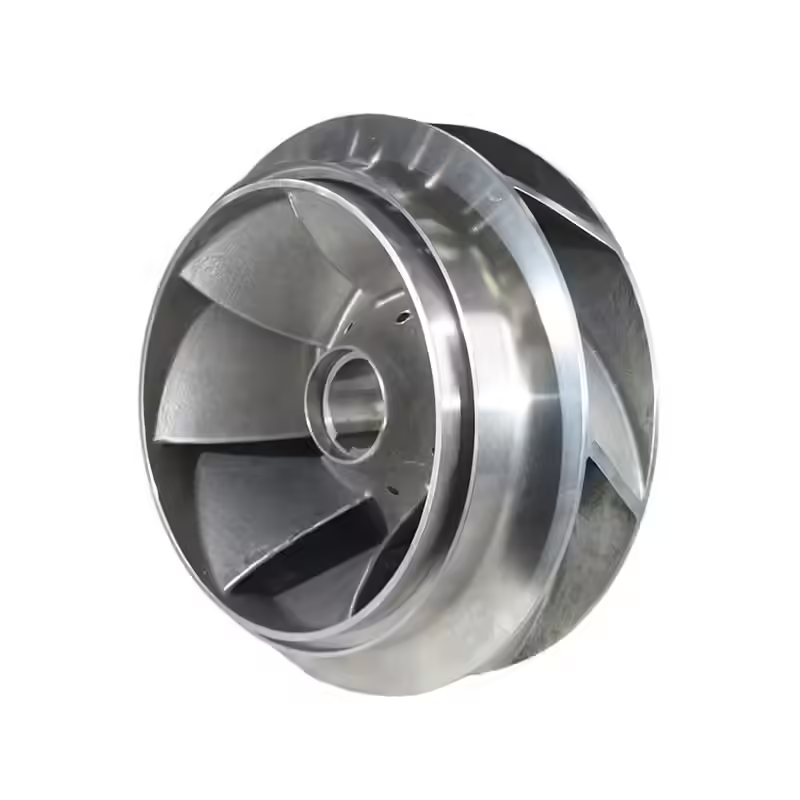
Casting impellers are indispensable components in a wide range of industrial applications, including pumps, compressors, and turbines. Their design and performance play a pivotal role in determining the overall efficiency, reliability, and durability of the equipment they are integrated into. Whether it’s facilitating fluid movement in water treatment systems, enhancing airflow in HVAC systems, or driving energy generation in power plants, these components are at the heart of many critical processes.
In this blog, we will delve into the six key features that define a high-performance casting impeller. These features are essential for ensuring optimal functionality, longevity, and operational efficiency. From precision engineering and advanced material selection to rigorous testing and maintenance considerations, each aspect contributes to the impeller’s ability to perform under demanding conditions.
By understanding these features, engineers, manufacturers, and end-users can make informed decisions that enhance the performance of their equipment. Whether you’re designing a new system or optimizing an existing one, this exploration will provide valuable insights into what makes a casting impeller truly high-performing. Join us as we uncover the elements that set exceptional impellers apart and ensure they meet the challenges of modern industrial applications.
Material Selection for Casting Impeller
The choice of material is paramount in determining the performance and lifespan of a casting impeller. Materials must be selected based on the specific application, considering factors such as corrosion resistance, strength, and thermal stability. Common materials include stainless steel, aluminum, and titanium, each offering unique benefits.
Stainless steel is widely used due to its excellent corrosion resistance and strength. Aluminum, on the other hand, is preferred for its lightweight properties, making it ideal for high-speed applications. Titanium is chosen for its exceptional strength-to-weight ratio and resistance to extreme temperatures. The right material ensures the casting impeller can withstand the operational demands placed upon it.
Precision Engineering and Design
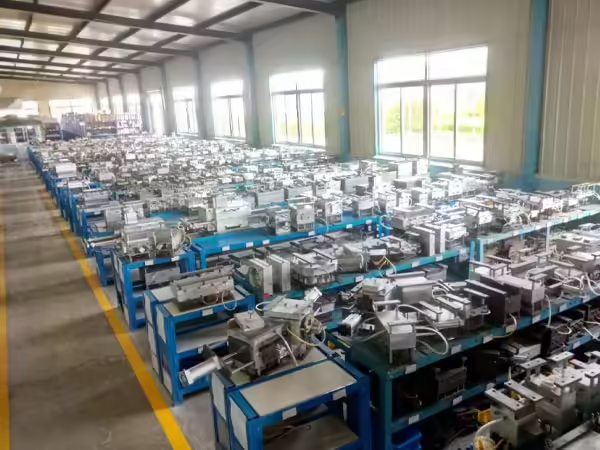
Precision engineering plays a pivotal role in the development of components that handle fluid dynamics, such as those found in turbomachinery. The geometry of these components, including blade shape, angle, and number, must be meticulously calculated to optimize fluid flow and minimize energy losses. Advanced computational fluid dynamics (CFD) simulations are often employed to achieve the most efficient design, ensuring that the final product meets stringent performance criteria.
The design process also involves ensuring uniform wall thickness to prevent stress concentrations and potential failure points. High-performance components in this category are characterized by their ability to maintain consistent performance under varying operational conditions, thanks to their precise engineering. This level of detail in design not only enhances efficiency but also extends the operational lifespan of the component.
Manufacturing Process and Quality Control
The manufacturing process of such components involves several stages, each requiring stringent quality control measures. The casting process itself must be carefully monitored to avoid defects such as porosity, inclusions, and shrinkage. Techniques such as investment casting and sand casting are commonly used, each with its own set of advantages, depending on the specific requirements of the component being produced.
Post-casting processes, including machining, heat treatment, and surface finishing, are equally important. These steps ensure the component meets the required dimensional tolerances and surface quality. Rigorous quality control checks, including non-destructive testing (NDT) methods, are essential to verify the integrity of the final product. These measures are crucial to ensure that the component can withstand the demanding conditions it will face in its intended application.
Performance Testing and Validation
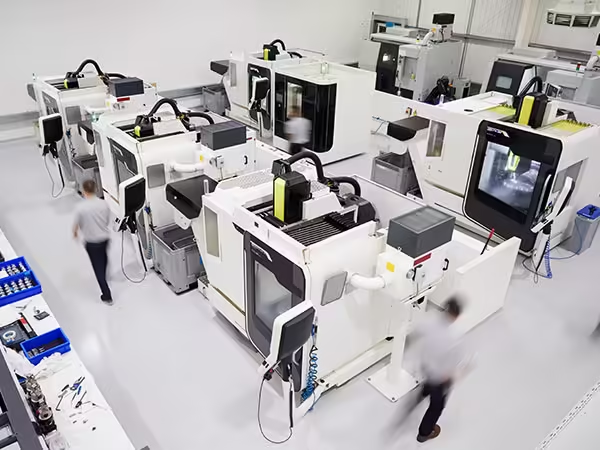
Before a component is deemed ready for use, it must undergo extensive performance testing. This includes hydrodynamic testing to evaluate its efficiency, flow rate, and pressure capabilities. Testing is conducted under various operating conditions to simulate real-world scenarios, ensuring that the component performs reliably in its intended environment.
Validation also involves assessing the component’s resistance to wear, corrosion, and fatigue. High-performance components are those that consistently meet or exceed the performance criteria set forth during the testing phase. This ensures reliability and efficiency in their intended applications, providing confidence that the component will perform as expected over its operational lifespan.
By focusing on precision engineering, meticulous manufacturing processes, and rigorous testing, manufacturers can produce components that meet the highest standards of quality and performance. This comprehensive approach ensures that the final product is not only efficient but also durable and reliable, capable of meeting the demands of its intended application.
Maintenance and Longevity
Proper maintenance is essential to extending the lifespan of critical components used in fluid-handling systems, such as those found in pumps and turbines. Regular inspections are a cornerstone of effective maintenance, as they help identify early signs of wear, corrosion, or damage, allowing for timely intervention before issues escalate. Key maintenance practices include thorough cleaning to remove debris or buildup, proper lubrication to reduce friction and wear, and alignment checks to ensure smooth and efficient operation. These measures not only preserve the component’s functionality but also enhance its overall performance and reliability.
The longevity of such components is heavily influenced by their initial design and the materials used in their construction. High-performance designs prioritize durability and efficiency, incorporating features that reduce stress concentrations and resist wear under demanding conditions. Material selection is equally critical; advanced alloys and coatings are often employed to enhance resistance to corrosion, erosion, and fatigue. By combining robust design with high-quality materials, manufacturers can create components that require minimal maintenance while delivering a maximized operational lifespan.
Reducing maintenance requirements is a significant advantage, as it directly translates to lower downtime and operational costs. For industries relying on continuous operation, such as water treatment, oil and gas, or chemical processing, this reliability is crucial. Components engineered for longevity not only improve operational efficiency but also contribute to sustainability by reducing the need for frequent replacements and minimizing resource consumption.
In addition to routine maintenance, predictive maintenance techniques are increasingly being adopted to further enhance component lifespan. By leveraging data from sensors and monitoring systems, operators can predict potential failures and address them proactively. This approach ensures that components remain in optimal condition, extending their service life and maintaining peak performance.
Ultimately, the combination of thoughtful design, high-quality materials, and proactive maintenance practices ensures that these critical components can withstand the rigors of their operating environments. This holistic approach not only maximizes their lifespan but also enhances the overall efficiency and reliability of the systems in which they are used.
Comparative Analysis of Casting Impeller Bahan
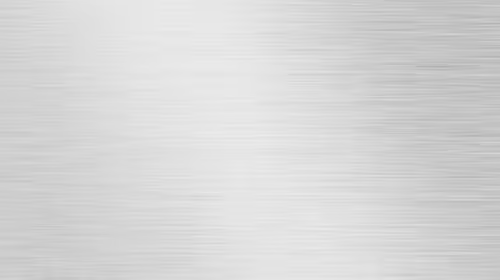
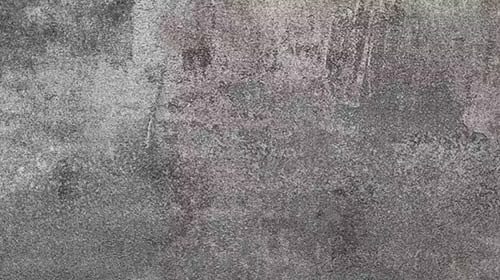
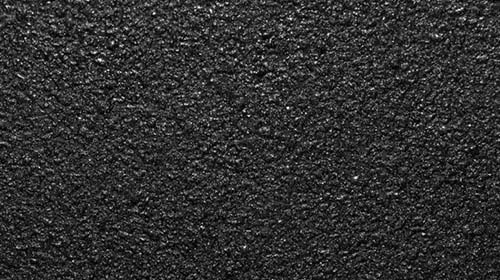
The following table provides a comparative analysis of the most commonly used materials for casting impellers, highlighting their key properties and typical applications.
bahan | Rintangan Kakisan | Strength | Weight | Thermal Stability | Typical Applications |
---|---|---|---|---|---|
Keluli Tahan Karat | tinggi | tinggi | Medium | tinggi | Pumps, Compressors |
Aluminum | Medium | Medium | rendah | Medium | High-Speed Applications |
Titanium | Very High | Very High | rendah | Very High | Aerospace, Extreme Conditions |
Kesimpulan
High-performance casting impellers are integral to the efficiency and reliability of various industrial equipment. By focusing on material selection, precision engineering, manufacturing quality, performance testing, and maintenance, one can ensure the optimal performance and longevity of these critical components. Understanding the key features that define a high-performance casting impeller allows for informed decision-making and improved operational outcomes.
Soalan Lazim
What is a casting impeller?
A casting impeller is a crucial component used in fluid machinery, such as pumps, compressors, and turbines. Its primary function is to transfer energy from the motor to the fluid, thereby enhancing flow rate and pressure. By rotating at high speeds, the impeller accelerates the fluid, enabling it to move through the system efficiently. This makes it an essential part of many industrial and commercial applications, including water treatment, HVAC systems, and energy generation. The design and quality of the impeller directly influence the overall performance and efficiency of the equipment it powers.
Why is material selection important for a casting impeller?
Material selection is a critical factor in the performance and durability of a casting impeller. The chosen material determines the impeller’s ability to withstand harsh operating conditions, such as exposure to corrosive fluids, high temperatures, and mechanical stress. For instance, materials with high corrosion resistance are essential for applications involving seawater or chemicals, while those with superior strength and thermal stability are required for high-pressure or high-temperature environments. The right material not only enhances the impeller’s performance but also extends its operational lifespan, reducing the need for frequent replacements and maintenance.
What are the common materials used for casting impellers?
Common materials include stainless steel, aluminum, and titanium, each offering unique benefits based on the application.
How does precision engineering affect a casting impeller?
Precision engineering plays a vital role in optimizing the performance of a casting impeller. By carefully designing the impeller’s geometry, including blade shape, angle, and number, engineers can maximize fluid dynamics and minimize energy losses. Advanced techniques such as computational fluid dynamics (CFD) simulations are often used to refine the design, ensuring the impeller operates efficiently under various conditions. Precision engineering also ensures uniform wall thickness, reducing stress concentrations and potential failure points. The result is a high-performance impeller that delivers consistent and reliable operation, even in demanding environments.
What maintenance practices are recommended for casting impellers?
Regular inspections, cleaning, lubrication, and alignment checks are essential to maintain the performance and extend the lifespan of casting impellers.
Kategori Produk
- Bahagian Injap
- Bahagian Pam Air
- Bahagian Kotak Galas
- Bahagian Die Casting
- Produk Pam Keluli Tahan Karat
- Produk Pam Besi Tuang
- Bahagian Injap Untuk Kegunaan Kereta
- Bahagian Kenderaan
- Bahagian Injap Untuk Kegunaan Awam
- Bahagian Pam Vakum KF
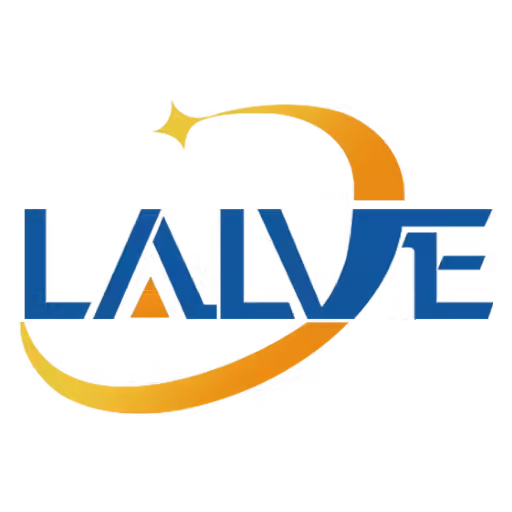