5 Common Mistakes When Choosing Precision Casting Impellers
Selamat Datang ke Blog Saya!
I’m thrilled to have you here! Before we dive into the content, I’d love for you to join me on my social media platforms. It’s where I share extra insights, connect with our amazing community, and keep you updated on the latest news. Here’s how you can stay connected:
📘 Facebook: Shanghai Leierwo Industry Trade Co., Ltd.
Now, let’s embark on this journey together! I hope you find the content here not only insightful but also inspiring and valuable. Let’s get started!
Jadual Kandungan
pengenalan
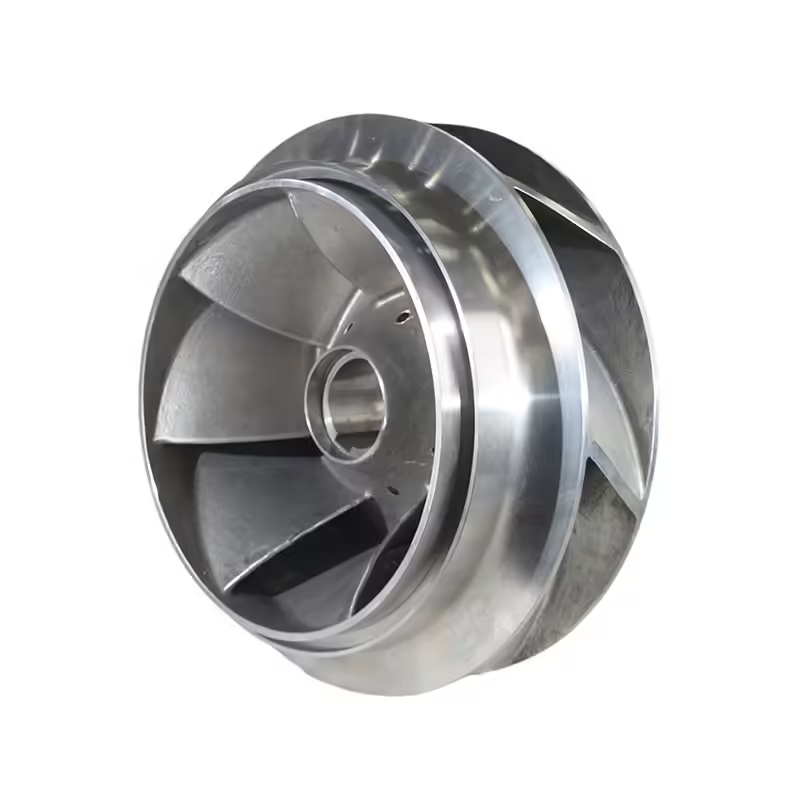
When it comes to selecting a precision casting impeller for industrial applications, making the right choice is crucial. The impeller plays a vital role in pumps, compressors, and turbines, affecting efficiency, durability, and overall performance. However, many buyers and engineers make avoidable mistakes when choosing precision casting impellers, leading to operational inefficiencies and increased costs.
In this blog, we will explore five common mistakes and how to avoid them. Whether you’re in aerospace, chemical processing, or water treatment, understanding these pitfalls will help you make an informed decision.
Mistake 1: Ignoring Material Compatibility
Why Material Selection Matters for Precision Casting Impellers
One of the most frequent errors is overlooking the material compatibility of a precision casting impeller with the working environment. Different applications require different alloys—such as stainless steel, aluminum, or titanium—to resist corrosion, erosion, and high temperatures.
For example:
- Chemical processing requires corrosion-resistant alloys like Hastelloy or Duplex stainless steel.
- Marine applications demand high resistance to saltwater corrosion.
- High-temperature environments need materials like Inconel.
Choosing the wrong material can lead to premature failure, increased maintenance costs, and even safety hazards.
Mistake 2: Overlooking Design Specifications
The Critical Role of Precision in Impeller Design
A precision casting impeller must adhere to exact design specifications to achieve optimal fluid dynamics and operational efficiency. The manufacturing process of precision casting allows for complex geometries, but this advantage can be negated if proper design considerations aren’t implemented. Common design-related oversights include:
- Incorrect blade geometry – Affects flow efficiency and pressure distribution.
- Improper hub-to-tip ratio – Can cause cavitation or excessive wear.
- Insufficient surface finish – Increases friction and reduces efficiency.
Working closely with engineers and manufacturers to validate design parameters ensures the impeller performs as intended.
Mistake 3: Choosing Based on Price Alone
Balancing Cost and Quality in Precision Casting Impellers
While initial cost is an important factor, selecting a precision casting impeller based solely on price can lead to significant long-term expenses. The hidden costs of cheaper alternatives often include:
- Material quality – Leading to faster degradation.
- Manufacturing precision – Resulting in inefficiencies.
- Ketahanan – Increasing replacement frequency.
A cost-benefit analysis should consider long-term operational savings rather than just upfront expenses.
Mistake 4: Neglecting Supplier Expertise
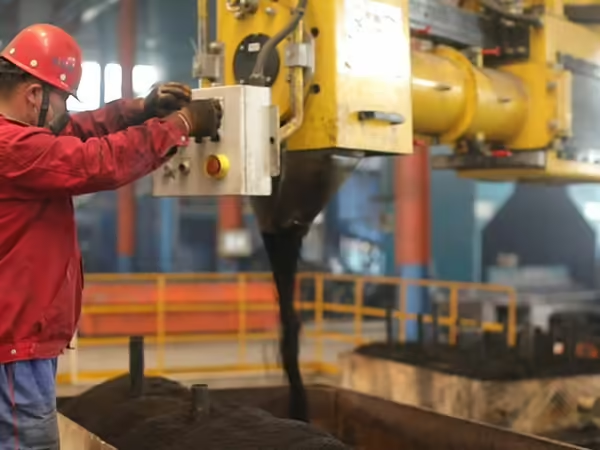
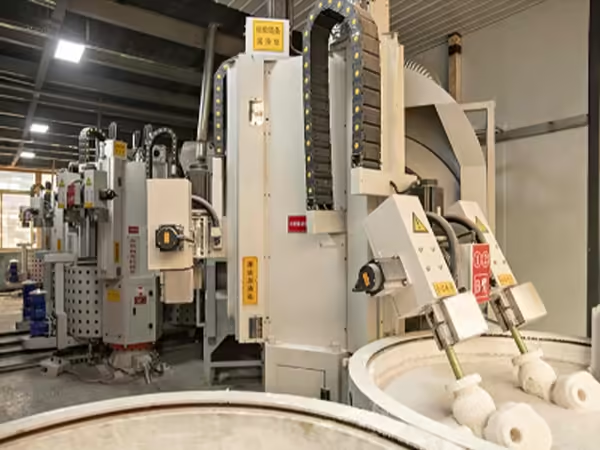
Why Supplier Experience Matters in Precision Casting
The quality and performance of a precision casting impeller are directly influenced by the manufacturer’s technical capabilities and quality systems. Key evaluation criteria should include:
- Industry experience – Look for suppliers with a proven track record.
- Quality certifications – ISO 9001, AS9100, or NADCAP compliance.
- Testing capabilities – Non-destructive testing (NDT) and performance validation.
A reputable supplier ensures higher consistency, reliability, and adherence to specifications.
Mistake 5: Skipping Performance Testing
The Role of Testing in Precision Casting Impeller Selection
Even a well-designed precision casting impeller must undergo rigorous testing before deployment. Common tests include:
- Hydrodynamic performance testing – Ensures flow efficiency.
- Material integrity checks – Detects casting defects.
- Fatigue and stress testing – Validates long-term durability.
Skipping these tests increases the risk of operational failures.
Comparison of Common Precision Casting Impeller Materials
To help you make an informed decision, here’s a comparison of popular materials used for precision casting impellers:
bahan | Rintangan Kakisan | Temperature Range | Aplikasi Biasa |
---|---|---|---|
Stainless Steel 316 | tinggi | -50°C to 400°C | Chemical processing, marine |
Aluminum Alloy | Sederhana | -100°C to 150°C | Aerospace, automotive |
Titanium | Cemerlang | -250°C to 600°C | Aerospace, medical, marine |
Inconel 718 | Very High | -200°C to 700°C | Oil & gas, high-temperature pumps |
This table highlights key considerations when selecting the right material for your precision casting impeller.
Kesimpulan
Choosing the right precision casting impeller requires careful consideration of material, design, cost, supplier expertise, and testing. Avoiding these five common mistakes will help you optimize performance, reduce downtime, and extend the lifespan of your equipment.
Always consult with experienced engineers and suppliers to ensure your selection meets the specific demands of your application.
Soalan Lazim
What is a precision casting impeller?
A precision casting impeller is a critical rotating component manufactured through investment casting processes that enables exceptional dimensional accuracy and surface finish quality. These impellers are commonly used in centrifugal pumps, compressors, and turbines where tight tolerances (typically within ±0.25mm) and optimized hydraulic performance are required. The precision casting process allows for complex blade geometries that would be difficult or impossible to achieve through conventional machining, making it ideal for high-efficiency fluid handling applications across industries like chemical processing, power generation, and marine propulsion.
How do I know which material is best for my application?
Selecting the optimal material for your precision casting impeller requires careful consideration of multiple operational factors including the pumped fluid’s chemical composition, operating temperature range, system pressure requirements, and potential corrosion mechanisms. Common material choices include stainless steel (316L or 17-4PH) for general corrosion resistance, duplex steels for chloride environments, nickel alloys like Inconel for high-temperature service, and titanium for seawater applications. Material engineers can perform corrosion testing and finite element analysis to recommend the most suitable alloy that balances performance requirements with cost considerations for your specific precision casting impeller application.
Can a precision casting impeller be customized?
Yes, reputable manufacturers offer custom designs tailored to specific flow dynamics, pressure requirements, and environmental conditions.
What are the signs of a failing impeller?
Common signs include reduced efficiency, unusual vibrations, increased noise, and visible wear or corrosion.
How often should a precision casting impeller be inspected?
The inspection frequency for a precision casting impeller should be determined based on the severity of service conditions, with typical intervals ranging from quarterly for aggressive applications to annually for clean service. Critical factors influencing inspection schedules include the abrasiveness of handled fluids, presence of corrosive elements, operating speed, and historical performance data. Many operators incorporate precision casting impeller inspections into their predictive maintenance programs, using vibration analysis, performance trending, and periodic disassembly examinations to assess condition. More frequent inspections may be warranted following process changes or if operating conditions approach design limits.
Kategori Produk
- Bahagian Injap
- Bahagian Pam Air
- Bahagian Kotak Galas
- Bahagian Die Casting
- Produk Pam Keluli Tahan Karat
- Produk Pam Besi Tuang
- Bahagian Injap Untuk Kegunaan Kereta
- Bahagian Kenderaan
- Bahagian Injap Untuk Kegunaan Awam
- Bahagian Pam Vakum KF
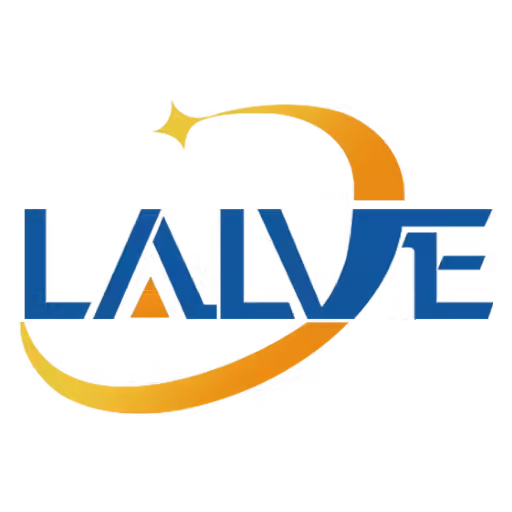