5 Hidden Traps to Avoid When Buying Hydraulic Valve Castings
Selamat Datang ke Blog Saya!
I’m thrilled to have you here! Before we dive into the content, I’d love for you to join me on my social media platforms. It’s where I share extra insights, connect with our amazing community, and keep you updated on the latest news. Here’s how you can stay connected:
📘 Facebook: Shanghai Leierwo Industry Trade Co., Ltd.
Now, let’s embark on this journey together! I hope you find the content here not only insightful but also inspiring and valuable. Let’s get started!
Jadual Kandungan
pengenalan
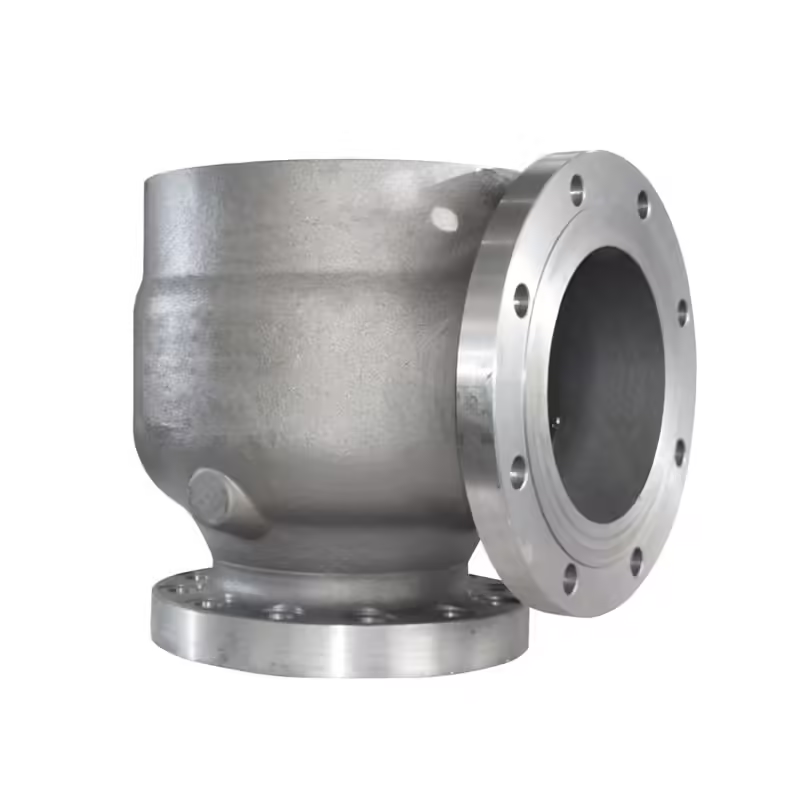
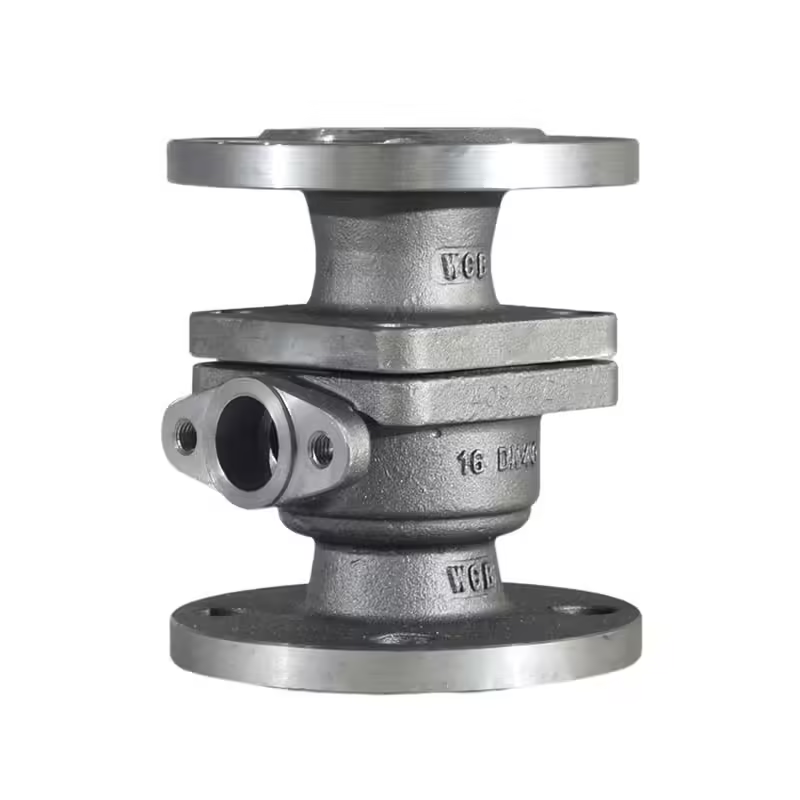
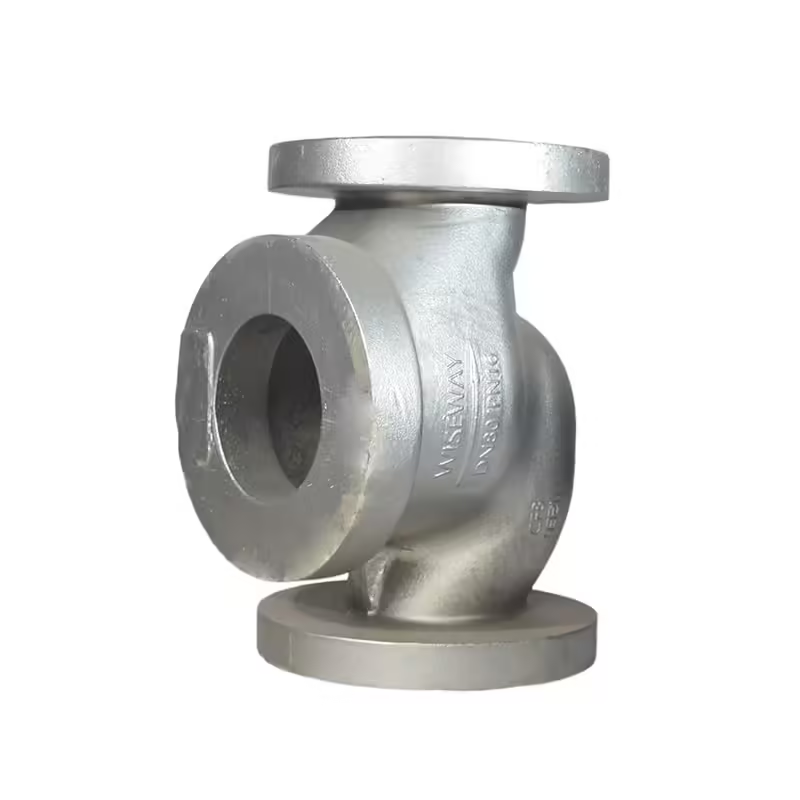
Hydraulic valve castings are critical components in industries such as oil & gas, construction, agriculture, and heavy machinery. Choosing the right supplier ensures durability, efficiency, and cost-effectiveness. However, buyers often fall into common traps that lead to poor-quality castings, project delays, or unexpected costs.
In this guide, we’ll uncover five hidden risks when purchasing hydraulic valve castings and how to avoid them. Whether you’re sourcing for OEM production or custom applications, this knowledge will help you make informed decisions.
NO 1. Ignoring Material Compatibility
One of the biggest mistakes buyers make is overlooking the material grade of hydraulic valve castings. Different applications require specific alloys—such as carbon steel, stainless steel, or ductile iron—to withstand pressure, corrosion, and wear.
Key Considerations:
- Pressure & Temperature Ratings – Ensure the material can handle operational stress.
- Corrosion Resistance – Critical for marine, chemical, or offshore applications.
- Machinability – Some alloys are easier to machine post-casting.
Common Materials for Hydraulic Valve Castings
Material Type | Best For | Limitations |
---|---|---|
Keluli Karbon | High-pressure systems | Prone to rust without coating |
Keluli Tahan Karat | Corrosive environments | Higher cost |
Ductile Iron | Cost-effective solutions | Lower impact resistance |
Choosing the wrong material can lead to premature failure, leaks, or safety hazards. Always consult with your supplier to match the alloy to your application.
NO 2. Overlooking Dimensional Accuracy
Hydraulic valve castings must fit precisely within complex systems. Even minor deviations can cause leaks, misalignment, or valve failure.
Why Tolerances Matter:
- Interchangeability – Ensures compatibility with existing components.
- Fluid Dynamics – Affects flow efficiency and pressure control.
- Regulatory Compliance – Some industries have strict standards.
How to Avoid This Trap:
- Request 3D scans or CMM reports for critical dimensions.
- Confirm if the supplier follows ISO 8062 or ASTM A703 standards.
- Ask for pre-production samples to verify fitment.
NO 3. Choosing Price Over Quality
While cost is important, selecting the cheapest hydraulic valve castings often leads to:
- Porosity defects (weak spots causing leaks)
- Inconsistent heat treatment (reducing strength)
- Poor surface finish (increasing wear)
Smart Cost-Saving Strategies:
- Bulk orders – Lower per-unit costs without sacrificing quality.
- Near-net-shape casting – Reduces machining expenses.
- Long-term supplier partnerships – Better pricing with reliable vendors.
Tip: Always compare quotes with quality certifications rather than just the lowest bid.
NO 4. Failing to Verify Supplier Certifications
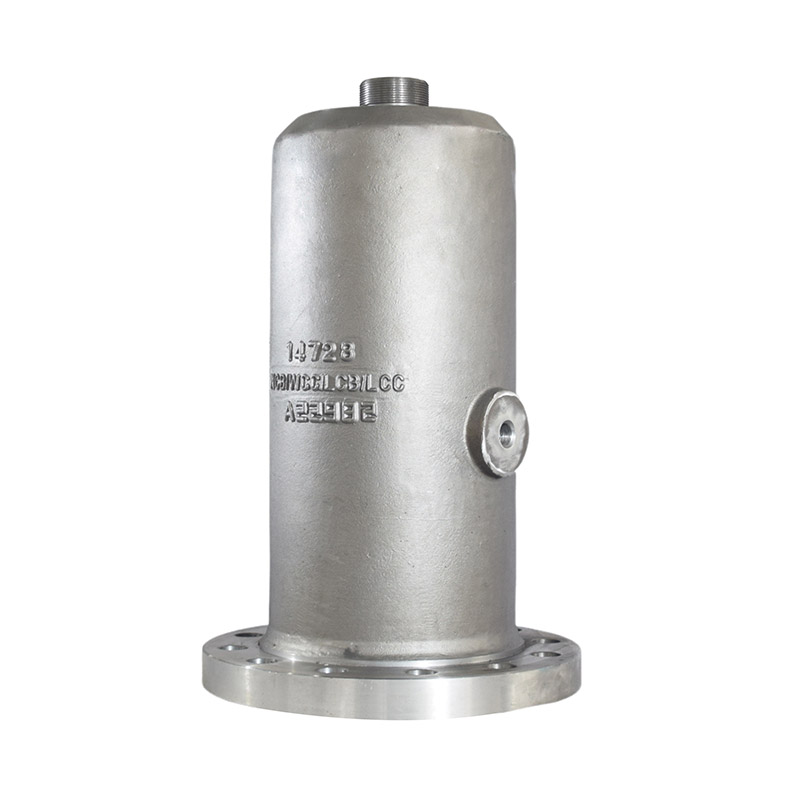
Not all foundries meet industry standards. A lack of certifications can mean:
- Unreliable material properties
- Poor traceability (no records of material origins)
- Non-compliance with safety regulations
Must-Have Supplier Certifications:
- ISO 9001:2015 (Quality Management)
- IATF 16949:2016 (Automotive Standards)
- PED 2014/68/EU (Pressure Equipment Directive)
Ask for:
- Material test reports (MTRs)
- X-ray or ultrasonic inspection results
- Pressure testing data
NO 5. Neglecting Post-Casting Machining
Many buyers assume hydraulic valve castings are ready to install. However, most require:
- CNC machining (for precise threading/sealing surfaces)
- Heat treatment (to enhance hardness)
- Surface coatings (for corrosion resistance)
Critical Post-Casting Processes:
Process | Purpose |
---|---|
CNC Machining | Ensures sealing surfaces meet specs |
Letupan Tembakan | Removes residue & improves fatigue life |
Electroplating | Adds corrosion-resistant layers |
Work with suppliers who offer end-to-end services—from casting to finishing—to avoid delays.
Why Choose Shanghai Leierwo?
At Shanghai Leierwo Industry & Trade Co., Ltd., we specialize in high-precision hydraulic valve castings using:
- Investment casting, sand casting & CNC machining
- Strict ISO 9001 & IATF 16949 certified processes
- Custom solutions with 3-5 week lead times
- Free samples & full inspection reports
With 18+ years of expertise, we help global clients avoid these common pitfalls.
Kesimpulan
Purchasing hydraulic valve castings requires careful attention to material selection, tolerances, supplier reliability, and post-processing. By avoiding these five traps, you’ll secure high-performance components that enhance system longevity and efficiency.
Soalan Lazim
Q1: What materials are best for high-pressure hydraulic valve castings?
A: For standard high-pressure applications, carbon steel (ASTM A216) offers excellent strength at a competitive price point. When corrosion resistance is required, stainless steel (CF8M) is the preferred choice. In more demanding environments involving extreme pressures or corrosive media, we recommend upgrading to duplex stainless steel or nickel-based alloys like Inconel. Our engineers can help select the optimal material based on your specific pressure ratings, temperature ranges, and fluid compatibility requirements.
Q2: How do I check casting quality before mass production?
A: We provide comprehensive quality verification including material certifications, dimensional inspection reports, and non-destructive testing results. Customers receive sample castings for evaluation along with detailed test reports documenting chemical composition, mechanical properties, and pressure test results. Third-party inspections are welcome to validate our quality control processes before full production begins.
Q3: Can Leierwo handle complex hydraulic valve casting designs?
A: Yes, our foundry specializes in complex valve castings with intricate geometries and tight tolerances. We utilize advanced investment casting techniques capable of producing thin-wall sections and complex internal passages. Our engineering team offers design-for-manufacturability consultations to optimize your components for casting production while maintaining performance requirements.
Q4: What’s the typical lead time for custom hydraulic valve castings?
A: Standard lead times range from 3-5 weeks depending on order quantity and complexity. The process includes pattern making, sample production, testing/approval, and final production. We maintain flexibility to accommodate urgent requests through expedited production scheduling and priority processing when needed.
Q5: Do you provide machining after casting?
A: We offer complete post-casting services including precision CNC machining, heat treatment, and specialized surface finishes. Our in-house machining capabilities ensure perfect dimensional accuracy for sealing surfaces and critical interfaces. This integrated approach guarantees better quality control and faster turnaround compared to using multiple vendors for casting and machining.
Kategori Produk
- Bahagian Injap
- Bahagian Pam Air
- Bahagian Kotak Galas
- Bahagian Die Casting
- Produk Pam Keluli Tahan Karat
- Produk Pam Besi Tuang
- Bahagian Injap Untuk Kegunaan Kereta
- Bahagian Kenderaan
- Bahagian Injap Untuk Kegunaan Awam
- Bahagian Pam Vakum KF
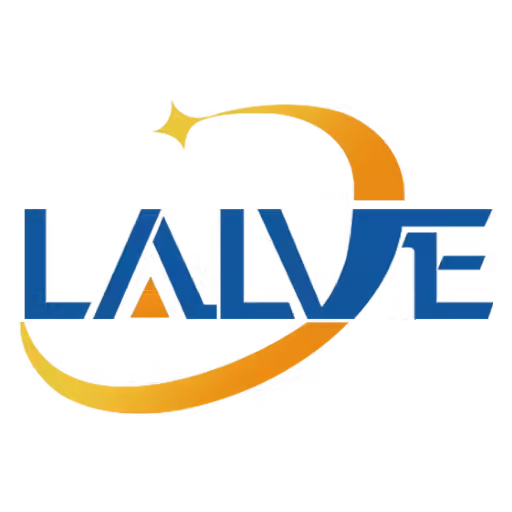