7 Best Practices for Valve Castings Design
Welcome to My Blog!
I’m thrilled to have you here! Before we dive into the content, I’d love for you to join me on my social media platforms. It’s where I share extra insights, connect with our amazing community, and keep you updated on the latest news. Here’s how you can stay connected:
📘 Facebook: Shanghai Leierwo Industry Trade Co., Ltd.
Now, let’s embark on this journey together! I hope you find the content here not only insightful but also inspiring and valuable. Let’s get started!
Table of Contents
Introduction
Valve castings are a critical component in various industries, including oil and gas, water treatment, and manufacturing. The design of these castings plays a pivotal role in ensuring their performance, durability, and efficiency. In this blog, we will explore seven best practices for valve castings design, providing insights into how to optimize this process for superior results. Whether you’re an engineer, designer, or industry professional, these guidelines will help you enhance the quality and functionality of valve castings.
Understanding Valve Castings
Before diving into the design practices, it’s essential to understand what valve castings are and their significance. Valve castings are metal components formed through casting processes, used to create valves that control the flow of liquids and gases. They must withstand high pressures, temperatures, and corrosive environments, making their design a complex and crucial task.
Material Selection
The choice of material is one of the most critical aspects of valve castings design. DiffeThe choice of material is one of the most critical aspects of designing components for flow control systems. Different applications require specific materials to ensure optimal performance. Common options include stainless steel, cast iron, and bronze, each offering unique properties tailored to various operational conditions.
- Stainless Steel: Known for its resistance to corrosion, this material is ideal for environments where exposure to harsh chemicals or moisture is a concern.
- Cast Iron: With its high strength and durability, it is well-suited for high-pressure applications, making it a reliable choice for demanding industrial settings.
- Bronze: Often utilized in marine environments due to its exceptional resistance to saltwater corrosion, it ensures longevity in challenging conditions.
Selecting the appropriate material ensures that these components can withstand the specific demands they will encounter during their operational lifespan.
Precision in Design Specifications
Accuracy in design specifications is vital for valve castings. This includes dimensions, Accuracy in design specifications is vital for creating components that function flawlessly. This includes attention to dimensions, tolerances, and surface finishes. Poorly specified designs can lead to operational failures, increased costs, and significant production delays.
- Utilizing CAD software enables engineers to create detailed and precise designs, reducing the likelihood of errors.
- Collaborating closely with manufacturers ensures that the design is feasible and can be produced efficiently.
Precision in the design phase minimizes errors and ensures that the final product meets the required standards, delivering reliable performance in its intended application.
Incorporating Simulation and Testing
Simulation and testing are indispensable tools in the design process for flow control components. These techniques help identify potential issues before production begins, saving both time and resources.
- Finite Element Analysis (FEA): This method simulates stress and strain on the design, allowing engineers to identify weak points and improve structural integrity.
- Computational Fluid Dynamics (CFD): This tool analyzes fluid flow through the component, ensuring optimal performance under real-world conditions.
By leveraging these advanced tools, designers can refine their work and ensure that the final product meets the highest standards of performance and reliability.
Optimizing for Manufacturing Processes
Designing with manufacturing in mind is crucial for achieving efficiency and cost-effectiveness. The choice of casting method, such as sand casting or investment casting, should influence the design of the component.
- Simplifying geometries reduces manufacturing complexity, making the production process more streamlined and cost-effective.
- Ensuring proper draft angles facilitates easy mold removal, minimizing the risk of defects during production.
Optimizing the design for manufacturing not only reduces production challenges but also lowers costs, ensuring that the final product is both high-quality and economically viable.costs.
Ensuring Compliance with Industry Standards
To guarantee safety and reliability, components used in flow control systems must adhere to established industry standards. Organizations such as ASME, API, and ISO provide comprehensive guidelines covering design, material selection, and testing procedures.
- Familiarize Yourself with Relevant Standards: Engineers and designers should stay updated on the latest regulations and requirements that apply to their specific applications.
- Incorporate Standards into the Design Process: Integrating these guidelines early in the design phase ensures that the final product meets all necessary criteria.
Compliance with industry standards not only ensures regulatory approval but also enhances the operational reliability of the components, instilling confidence in end-users.
Addressing Corrosion and Wear Resistance
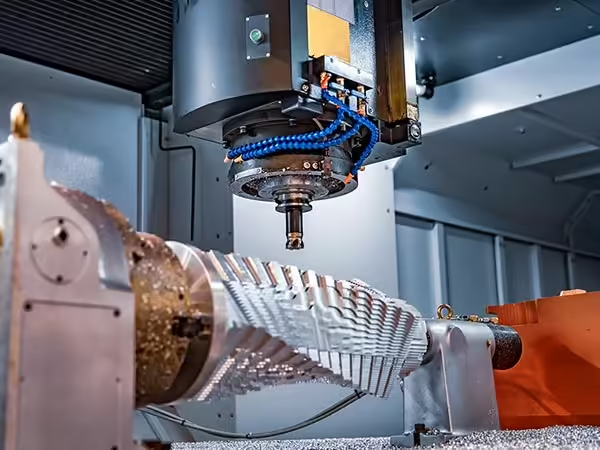
Corrosion and wear are significant challenges for metal components, particularly those exposed to harsh environments such as chemical processing, marine applications, or high-temperature settings. Designers must take proactive steps to mitigate these issues to ensure longevity and performance.
- Use Corrosion-Resistant Materials: Materials like stainless steel, duplex steel, or nickel alloys are excellent choices for environments prone to chemical or moisture exposure.
- Apply Protective Coatings or Treatments: Techniques such as galvanizing, anodizing, or applying epoxy coatings can significantly enhance the durability of the components.
By addressing these factors, engineers can improve the lifespan and functionality of the components, reducing maintenance costs and downtime in industrial applications.
Implementing Sustainable Design Practices
As sustainability becomes a priority in engineering and manufacturing, incorporating eco-friendly practices into the design process is essential. For flow control components, this involves selecting materials and processes that minimize environmental impact while maintaining performance.
- Select Recyclable Materials: Opting for materials that can be recycled at the end of their lifecycle reduces waste and promotes a circular economy.
- Minimize Material Waste During Production: Efficient design practices, such as optimizing geometries and using advanced manufacturing techniques, help reduce scrap and conserve resources.
Sustainable practices not only benefit the environment but also align with the growing demand for greener solutions from industries and consumers alike. By adopting these approaches, designers can create components that are both high-performing and environmentally responsible.
Comparative Analysis of Valve Castings Materials
Material | Advantages | Disadvantages | Best Use Cases |
---|---|---|---|
Stainless Steel | Corrosion-resistant, durable | Higher cost | Chemical, oil and gas |
Cast Iron | High strength, cost-effective | Prone to rust | Water treatment, manufacturing |
Bronze | Excellent for marine environments | Expensive, softer material | Marine, plumbing |
This table provides a quick comparison of common materials used in valve castings, helping designers make informed decisions.
Conclusion
Designing valve castings is a complex process that requires careful consideration of materials, precision, testing, and compliance with industry standards. By following these seven best practices, designers can create valve castings that are efficient, durable, and reliable. Incorporating sustainable practices and leveraging advanced tools like simulation further enhances the design process. Whether you’re working on a new project or improving an existing design, these guidelines will help you achieve superior results in valve castings design.
FAQ
Q1: What are the most common materials used in valve castings?
A1: The most common materials include stainless steel, cast iron, and bronze, each suited for specific applications.
Q2: How can simulation tools improve valve castings design?
A2: Simulation tools such as Finite Element Analysis (FEA) and Computational Fluid Dynamics (CFD) play a crucial role in enhancing the design process. FEA allows engineers to simulate stress and strain on the component, identifying potential weak points and ensuring structural integrity. CFD analyzes fluid flow through the component, optimizing its performance under real-world conditions. By using these tools, designers can identify and address potential issues early in the design phase, reducing the need for costly revisions during production. This not only saves time and resources but also ensures that the final product meets the highest standards of performance and reliability.
Q3: Why is compliance with industry standards important?
A3: Compliance ensures that valve castings meet safety, reliability, and operational requirements, reducing risks and liabilities.
Q4: What are some sustainable practices in valve castings design?
A4: Sustainable practices in the design process focus on minimizing environmental impact while maintaining performance and functionality. These practices include using recyclable materials, such as stainless steel or aluminum, which can be repurposed at the end of their lifecycle. Additionally, optimizing designs to reduce material waste during production helps conserve resources and lower manufacturing costs. Energy-efficient manufacturing processes, such as using renewable energy sources or implementing energy-saving technologies, further contribute to sustainability. By adopting these practices, manufacturers can create components that not only meet operational requirements but also align with broader environmental goals, appealing to eco-conscious customers and industries.
Q5: How can corrosion and wear resistance be improved?
A5: Improving corrosion and wear resistance is critical for components exposed to harsh environments, such as chemical processing, marine applications, or high-temperature settings. One effective approach is selecting materials inherently resistant to corrosion, such as stainless steel, duplex steel, or nickel alloys. Additionally, applying protective coatings or treatments, such as galvanizing, anodizing, or epoxy coatings, can significantly enhance the durability of the components. These measures help prevent degradation over time, reducing maintenance costs and extending the lifespan of the components. By addressing corrosion and wear resistance early in the design process, engineers can ensure that the components perform reliably in even the most challenging conditions.
Product Categories
- Valve Parts
- Water Pump Parts
- Bearing Box Parts
- Die Casting Parts
- Stainless Steel Pump Products
- Cast Iron Pump Products
- Valve Parts For Automobile Use
- Auto Parts
- Valve Parts For Civil Use
- Vacuum Pump Parts KF
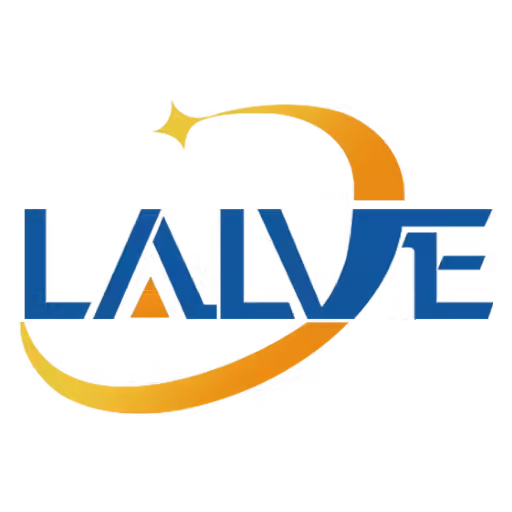