8 Terrifying Signs of Bearing Box Failure
Welcome to My Blog!
I’m thrilled to have you here! Before we dive into the content, I’d love for you to join me on my social media platforms. It’s where I share extra insights, connect with our amazing community, and keep you updated on the latest news. Here’s how you can stay connected:
📘 Facebook: Shanghai Leierwo Industry Trade Co., Ltd.
Now, let’s embark on this journey together! I hope you find the content here not only insightful but also inspiring and valuable. Let’s get started!
Table of Contents
Introduction
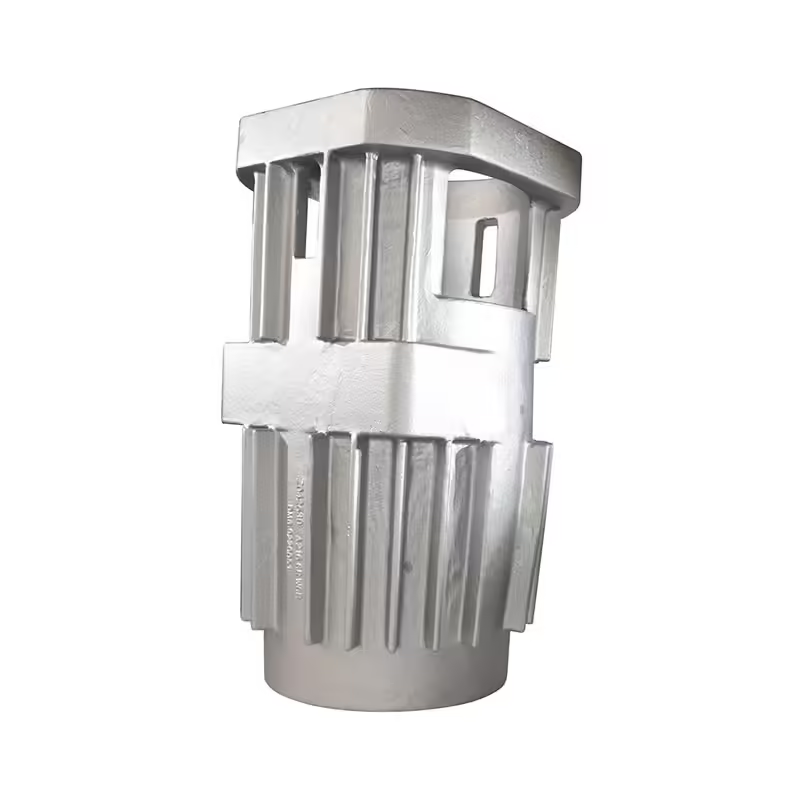
The bearing box is the unsung hero of industrial machinery, quietly ensuring smooth operation while protecting critical components from contamination and misalignment. When this vital component begins to fail, the consequences can be catastrophic – from unplanned downtime costing thousands per hour to complete equipment failure requiring expensive replacements.
In this comprehensive guide, we’ll examine the eight most alarming signs of bearing box failure that every maintenance professional should recognize. We’ll not only identify these warning signals but also provide practical solutions to address them before they escalate into major problems. Whether you’re managing a small manufacturing operation or a large industrial facility, understanding these failure symptoms could save your organization significant time and money.
NO 1. Unusual Noises: Your Bearing Box is Trying to Tell You Something
One of the earliest and most obvious indicators of bearing box trouble is abnormal noise. These sounds aren’t just annoyances – they’re critical warnings that demand immediate attention.
Common problematic sounds include:
- Grinding or growling noises that suggest insufficient lubrication or advanced bearing wear
- High-pitched squealing indicating misalignment or excessive friction
- Intermittent clicking or knocking sounds signaling loose components or damaged rolling elements
The progression of these sounds often follows a predictable pattern. What starts as a barely noticeable hum can develop into a concerning rumble before escalating to a terrifying grinding noise that signals imminent failure. The key is to investigate at the first sign of unusual sounds rather than waiting until the problem becomes severe.
NO 2. Excessive Vibration: More Than Just an Annoyance
Vibration is another critical warning sign that your bearing box may be failing. While some vibration is normal in rotating equipment, excessive or unusual vibration patterns often indicate underlying issues that need addressing.
Primary causes of problematic vibration include:
- Imbalance in rotating components
- Shaft or coupling misalignment
- Bearing wear or damage
- Loosening of mounting hardware
Modern vibration analysis tools can detect these issues at their earliest stages, often before they’re noticeable to human senses. Regular vibration monitoring should be part of any comprehensive predictive maintenance program.
NO 3. Overheating: When Your Bearing Box Runs Too Hot
Excessive heat is both a symptom and a cause of bearing box problems. Elevated temperatures accelerate lubricant breakdown and component wear, creating a vicious cycle that leads to premature failure.
Common causes of overheating include:
- Inadequate or degraded lubrication
- Excessive loading beyond design specifications
- Blocked cooling vents or passages
- Misalignment creating additional friction
Infrared thermography provides an excellent non-contact method for monitoring bearing box temperatures and identifying potential trouble spots before they lead to failure.
Critical Bearing Box Failure Factors
To better understand and prevent bearing box failures, consider these key factors:
Failure Factor | Early Warning Signs | Preventive Measures |
---|---|---|
Lubrication Issues | Increased temperature, discolored grease | Implement automatic lubrication systems |
Contamination | Noise fluctuations, rapid wear | Improve sealing, use desiccant breathers |
Misalignment | Uneven wear patterns, vibration | Laser alignment during installation |
Overloading | Premature fatigue, cracking | Verify load ratings, reduce side loads |
NO 4. Lubrication Leaks: More Than Just a Mess

Lubricant leaks from your bearing box are more than just a cleanliness issue – they’re a serious warning sign that demands immediate attention. Leaks can lead to inadequate lubrication, contamination ingress, and ultimately, catastrophic failure.
Common leak sources include:
- Worn or damaged seals
- Cracked or porous housing material
- Overpressurization of the bearing chamber
- Improperly installed components
Regular visual inspections can catch leaks early, and seal replacement programs can prevent them from occurring in the first place.
NO 5. Visible Damage: What Your Eyes Can Tell You
Sometimes the signs of bearing box trouble are literally staring you in the face. Regular visual inspections can reveal physical damage that indicates developing problems.
Look for:
- Rust or corrosion indicating moisture intrusion
- Cracks or deformation suggesting mechanical stress
- Scoring marks revealing abrasive contamination
- Discoloration pointing to overheating
Documenting these observations with photos over time can help track the progression of issues and determine appropriate intervention points.
NO 6. Increased Energy Consumption: The Hidden Cost of Failure
A failing bearing box doesn’t just announce its problems through obvious symptoms – it also silently drives up your energy costs. As friction increases due to developing issues, your motors must work harder to maintain the same output.
This manifests as:
- Gradual increases in amperage draw
- Higher electricity bills without increased production
- Reduced overall equipment efficiency
Monitoring energy consumption trends can help identify bearing box problems before they become severe, often paying for the monitoring effort through energy savings alone.
NO 7. Shaft Movement: When Things Get Loose
Excessive shaft movement is a serious warning sign that your bearing box is no longer providing proper support and alignment. This can lead to cascading failures throughout your machinery.
Indicators include:
- Visible wobble in rotating components
- Increased clearance when manually checking for play
- Uneven wear patterns on shafts and bearings
Regular checks for shaft movement, especially during routine maintenance, can catch these issues before they cause major damage.
NO 8. Sudden Stoppages: The Worst-Case Scenario
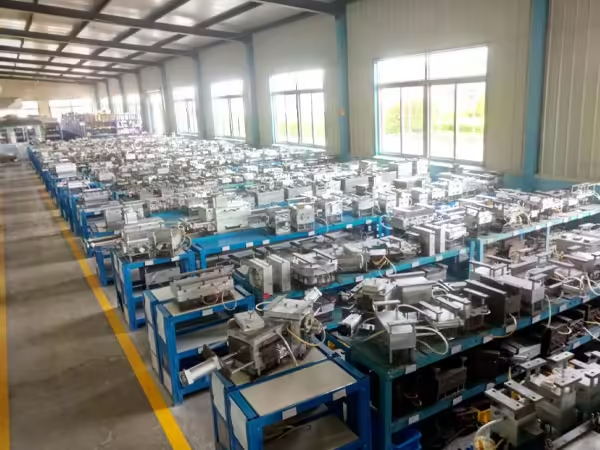
When all other warning signs are ignored, the final symptom is often a sudden, catastrophic failure that brings your equipment to an abrupt halt. These unplanned stoppages are the most expensive consequence of bearing box failure, often requiring:
- Emergency repair crews
- Overtime labor costs
- Lost production time
- Potential collateral damage to other components
The best solution is to never reach this point by addressing the earlier warning signs we’ve discussed.
Conclusion
Recognizing these eight terrifying signs of bearing box failure is the first step toward preventing costly downtime and repairs. By implementing a comprehensive monitoring program that includes:
- Regular visual inspections
- Vibration analysis
- Temperature monitoring
- Lubrication management
- Energy consumption tracking
you can catch developing issues early and address them before they escalate into major problems. Remember – the small investment in preventive maintenance pays enormous dividends in equipment reliability and operational efficiency.
FAQ
Q: How often should bearing boxes be lubricated?
A: Lubrication intervals vary based on operating conditions, but most industrial applications require relubrication every 3-6 months of continuous operation.
Q: Can vibration analysis really predict bearing box failures?
A: Yes, modern vibration analysis can detect developing bearing issues up to 6 months before catastrophic failure in many cases.
Q: What’s the most overlooked bearing box maintenance task?
A: Seal inspection and replacement is often neglected, leading to preventable contamination issues.
Q: How long should a properly maintained bearing box last?
A: With proper care, most industrial bearing boxes should provide 5-8 years of reliable service before requiring replacement.
Q: Are there any quick checks I can do daily?
A: A simple “touch test” for unusual heat and listening for abnormal sounds can catch many early-stage issues.
Product Categories
- Valve Parts
- Water Pump Parts
- Bearing Box Parts
- Die Casting Parts
- Stainless Steel Pump Products
- Cast Iron Pump Products
- Valve Parts For Automobile Use
- Auto Parts
- Valve Parts For Civil Use
- Vacuum Pump Parts KF
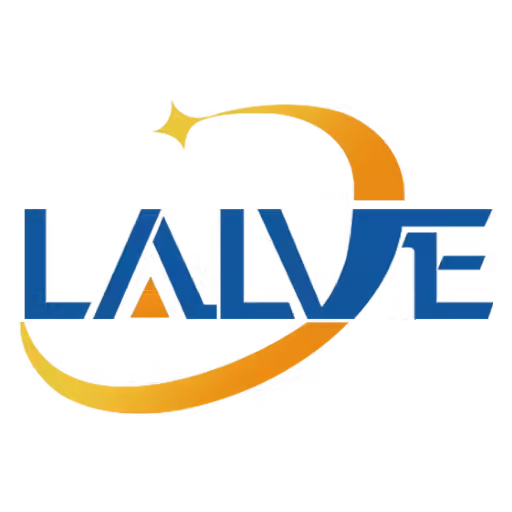