Investment Casting Services
Investment casting is a precision casting process known for producing high-quality, complex, and precise metal parts, offering advantages over methods like sand casting. It supports various materials, including aluminum alloys, copper alloys, and stainless steel, making it ideal for intricate and high-precision castings.
The use of wax patterns allows investment casting to capture fine details, enabling the production of components with complex features and tight tolerances, often reducing the need for additional machining. This method is particularly suitable for industries requiring precise and durable parts, such as aerospace, automotive, and medical sectors.
Additionally, investment casting is highly flexible, supporting both small-batch and large-scale production. Whether you need prototypes, custom designs, or specialized components, this process ensures consistent quality and reliability, making it a trusted solution for high-performance metal parts tailored to your needs.
The use of wax patterns allows investment casting to capture fine details, enabling the production of components with complex features and tight tolerances, often reducing the need for additional machining. This method is particularly suitable for industries requiring precise and durable parts, such as aerospace, automotive, and medical sectors.
Additionally, investment casting is highly flexible, supporting both small-batch and large-scale production. Whether you need prototypes, custom designs, or specialized components, this process ensures consistent quality and reliability, making it a trusted solution for high-performance metal parts tailored to your needs.
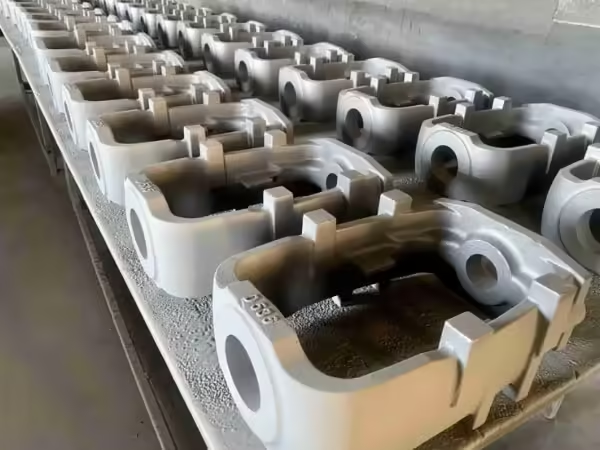
ISO9001:2015 Certified
12K+Precision Castings Produced Monthly
40+Different Casting Materials
50+Countries Shipped
Advantages of Investment Casting
Investment casting produces components with high surface precision and allows for complex shapes. It is an ideal choice for customers who require specific dimensional accuracy, smooth surface finishes, and the production of small to medium-sized components.
High Precision
Investment casting offers exceptional dimensional accuracy, with tolerances as tight as ±0.05mm, minimizing or eliminating the need for post-machining. It is ideal for precision components with strict requirements.
Customization
This process supports both small-batch and large-scale custom production. Parts can be manufactured based on customer-provided drawings or samples, ensuring tailored solutions for specific needs.
Smooth Surface Finish
Investment casting produces high-quality surface finishes, typically achieving Ra 1.6-3.2μm. This reduces the need for additional surface treatments, enhancing the appearance and functionality of the final product.
Design Freedom
The process allows for complex geometries, internal cavities, thin walls, and intricate details that are difficult to achieve with other casting methods. This provides greater flexibility in engineering design.
High-Quality Materials
Investment casting supports a wide range of high-performance materials, including stainless steel, carbon steel, alloy steel, and aluminum alloys. This ensures optimal material selection for various industrial applications.
Wide Size Range
Investment casting can produce parts ranging from a few grams to dozens of kilograms, making it suitable for various industries such as aerospace, automotive, medical, and machinery manufacturing.
Our Investment Casting Capabilities
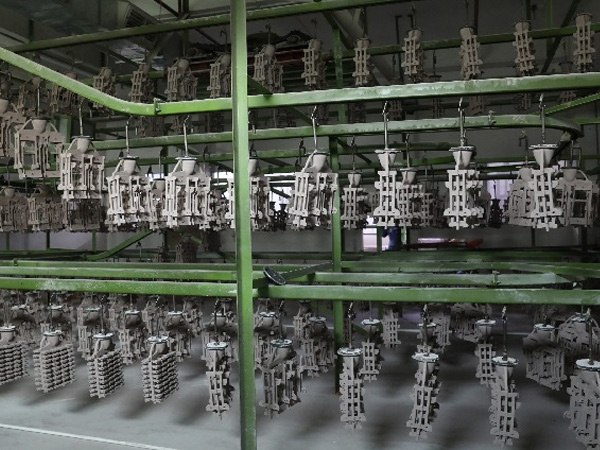
Water Glass Casting
Water glass investment casting, also known as water glass precision casting, is a widely used casting process that employs water glass (sodium silicate solution) as a binder combined with refractory materials to create molds for metal components. This cost-effective and high-precision method is extensively used in the automotive, machinery, and aerospace industries.
At Leierwo, our precision cast parts produced through the water glass casting process achieve general linear tolerances of ISO 8062 CT7-CT8 and a surface roughness of approximately Ra12.5. This casting method is commonly used for manufacturing excavator bucket teeth, adapters, truck components, and agricultural machinery parts.
At Leierwo, our precision cast parts produced through the water glass casting process achieve general linear tolerances of ISO 8062 CT7-CT8 and a surface roughness of approximately Ra12.5. This casting method is commonly used for manufacturing excavator bucket teeth, adapters, truck components, and agricultural machinery parts.
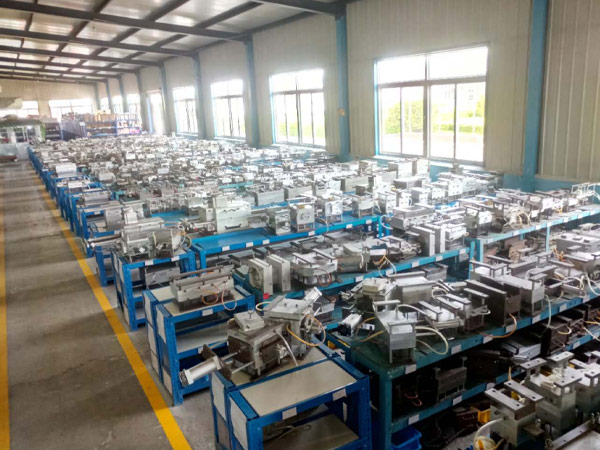
Silica Sol Casting
Silica sol casting is a high-precision investment casting process that uses silica sol as a binder, combined with precision mold technology, to produce metal parts with high accuracy and smooth surfaces. This casting method is widely used in aerospace, automotive, and medical device industries.
Leierwo utilizes the silica sol casting process to manufacture castings with an internal diameter tolerance of ISO 8062 CT4-CT6. The surface finish can reach Ra6.3. Compared to water glass casting, silica sol casting offers superior quality but comes at a higher cost. We primarily use this casting method for stainless steel castings and other precision steel components.
Leierwo utilizes the silica sol casting process to manufacture castings with an internal diameter tolerance of ISO 8062 CT4-CT6. The surface finish can reach Ra6.3. Compared to water glass casting, silica sol casting offers superior quality but comes at a higher cost. We primarily use this casting method for stainless steel castings and other precision steel components.
Investment Casting Materials
Leierwo meets the standards of ASTM, SAE, AISI, ACI, DIN, EN, ISO, and GB, offering casting capabilities for hundreds of ferrous and non-ferrous alloy materials. Our expertise includes stainless steel, alloy steel, copper alloys, aluminum alloys, nickel-based alloys, carbon steel, cast iron, and more.
Stainless Steel
Due to its excellent durability and corrosion resistance, stainless steel has become one of the most popular materials in investment casting production. At Leierwo, we can cast various types of stainless steel, including martensitic stainless steel, ferritic stainless steel, austenitic stainless steel, precipitation-hardened stainless steel, and duplex stainless steel.
Alloy Steel
Alloy steel castings are steel castings alloyed with elements such as molybdenum, manganese, nickel, chromium, vanadium, silicon, and boron. Precision-cast alloy steel parts offer enhanced strength, hardness, wear resistance, and toughness. Typical alloy steel grades for precision casting include AISI 4130, AISI 4140, AISI 8620, and AISI 8630.
Carbon Steel
Nickel-Based Alloys
Copper Alloys
Customizable Surface Treatment Options
Shot Blasting
Shot blasting is a surface treatment process that involves propelling abrasive materials at high speeds to remove surface contaminants, scale, or rust. This process enhances surface adhesion for subsequent coatings and improves fatigue resistance.
Machining
Machining is a precision process used to achieve tight tolerances and smooth surface finishes. It includes milling, turning, drilling, and grinding to meet specific dimensional and functional requirements.
Paint Coating
Paint coating provides a protective and decorative finish to alloy steel surfaces. It enhances corrosion resistance and allows for various color and texture options, making it ideal for aesthetic and functional purposes.
Powder Coating
Powder coating is a dry finishing process that creates a durable, wear-resistant, and corrosion-resistant surface. It offers a uniform appearance and is available in a variety of colors and textures.
Galvanized Coating
Galvanization involves applying a layer of zinc to the steel surface, offering excellent corrosion protection. Hot-dip galvanizing and electro-galvanizing are common methods used to extend the lifespan of steel components.
Black Oxide Coating
Black oxide treatment creates a thin, black protective layer on the steel surface to improve corrosion resistance and reduce light reflection. It is commonly used in automotive, aerospace, and tooling applications.
Start Your Project with Leierwo
1. Submit Your Inquiry
Send your CAD drawings and 3D files via email, specifying material grade, order quantity, surface finish, or any other relevant details.
2. Cost Calculation
Once we receive your design, our engineering team will carefully evaluate the drawings and calculate the price based on actual production costs as soon as possible.
3. Start Production
Upon pricing approval, our production team will prepare the materials and schedule production promptly. Leierwo always ensures on-time delivery.
4. Arrange Delivery
After production is completed, we will provide packaging details and arrange shipment via sea or air. We support global shipping for every order.
FAQ
Do you offer export services?
Why choose leierwo foundry for casting?
What is your production capacity? Do you accept custom orders?
What international standards do your castings comply with?
How do you ensure product quality?
What is your Minimum Order Quantity (MOQ)?
What is your lead time?
Can you provide samples?