Alloy Steel Castings
Alloy Steel Castings
Alloy steel castings refer to metal products made from various alloy steel materials through different casting processes. These castings are based on stainless steel castings, with additional elements incorporated into the raw materials to meet specific mechanical performance requirements. Compared to traditional metal casting with single-material steel, alloy steel casting—enhanced with elements such as manganese, nickel, chromium, vanadium, and molybdenum—significantly improves the material’s properties. It enhances strength, hardness, toughness, and wear resistance, making alloy steel castings ideal for demanding industrial applications.
Leierwo’s Expertise in Alloy Steel Castings
At Leierwo, we specialize in manufacturing high-performance alloy steel castings with superior strength, toughness, and corrosion resistance. Our advanced production capabilities and strict quality control ensure that every alloy steel casting meets the highest industry standards. Whether for heavy machinery, automotive components, or specialized industrial equipment, our alloy steel castings deliver exceptional performance and reliability.
Alloy steel castings refer to metal products made from various alloy steel materials through different casting processes. These castings are based on stainless steel castings, with additional elements incorporated into the raw materials to meet specific mechanical performance requirements. Compared to traditional metal casting with single-material steel, alloy steel casting—enhanced with elements such as manganese, nickel, chromium, vanadium, and molybdenum—significantly improves the material’s properties. It enhances strength, hardness, toughness, and wear resistance, making alloy steel castings ideal for demanding industrial applications.
Leierwo’s Expertise in Alloy Steel Castings
At Leierwo, we specialize in manufacturing high-performance alloy steel castings with superior strength, toughness, and corrosion resistance. Our advanced production capabilities and strict quality control ensure that every alloy steel casting meets the highest industry standards. Whether for heavy machinery, automotive components, or specialized industrial equipment, our alloy steel castings deliver exceptional performance and reliability.
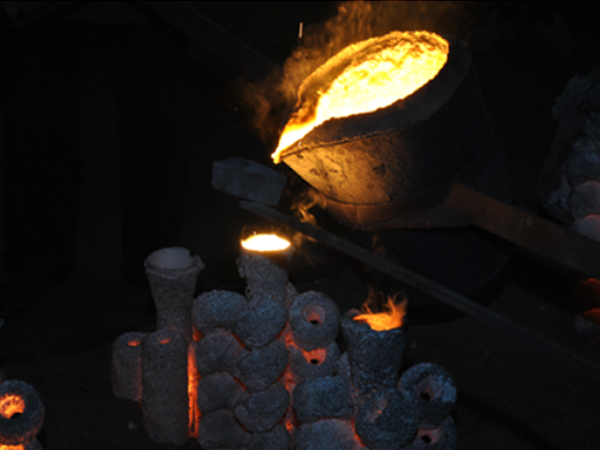
Common Alloy Steels for Casting
Grade | Carbon Content (%) | Silicon (%) | Manganese (%) | Chromium (%) | Molybdenum (%) | Phosphorus ≤ (%) | Sulfur ≤ (%) | Nickel (%) |
---|---|---|---|---|---|---|---|---|
42CrMo | 0.38-0.45 | 0.17-0.37 | 0.50-0.80 | 0.90-1.20 | 0.15-0.25 | – | – | – |
35CrMo | 0.32-0.40 | 0.17-0.37 | 0.40-0.70 | 0.80-1.10 | 0.15-0.25 | – | – | – |
40CrNiMo | 0.37-0.44 | 0.17-0.37 | 0.50-0.80 | 0.60-0.90 | 0.15-0.25 | – | – | 1.25-1.65 |
4130 | 0.28-0.33 | 0.15-0.35 | 0.40-0.60 | 0.80-1.10 | 0.15-0.25 | 0.035 | 0.04 | – |
4140 | 0.38-0.43 | 0.15-0.35 | 0.75-1.00 | 0.80-1.10 | 0.15-0.25 | 0.035 | 0.04 | – |
8630 | 0.28-0.33 | 0.15-0.35 | 0.70-0.90 | 0.40-0.60 | 0.15-0.25 | 0.035 | 0.04 | 0.40-0.70 |
If you are looking for a reliable alloy steel investment casting supplier in China, contact us today. We are happy to start our cooperation with a trial order at a competitive price.
Alloy Steel Investment Casting
We strictly follow Standard Operating Procedures (SOP) in every stage of our production process for alloy steel castings. The main steps include: pouring simulation, mold development for alloy steel castings, raw material inspection, wax pattern making, shell making, metal pouring for alloy steel castings, cleaning and heat treatment, inspection, warehouse packaging, and shipping of alloy steel castings.
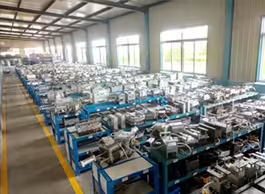
Mold Development
Our technical department develops the molds, while the quality department conducts dimensional inspections using a coordinate measuring machine (CMM).
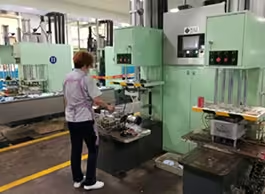
Wax Pattern
The workshop utilizes fully automated wax injection machines, which automatically set wax injection pressure, holding time, and other parameters to produce high-quality wax patterns.
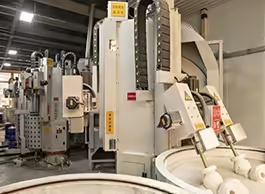
Shell Preparation
The workshop operates four automated production lines with an annual capacity of 1,800 shell molds. We monitor the humidity, temperature, and concentration of the aluminum chloride solution using hygrometers, barometers, and pH meters.
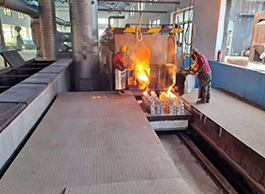
Metal Pouring
Currently, six 500KG furnaces are in production, with an additional four 500KG backup furnaces available for increased capacity. All operators undergo rigorous testing to ensure materials meet required specifications.
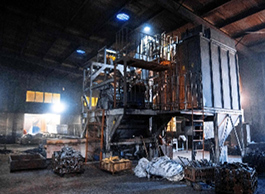
Cleaning & Heat Treatment
Our fully equipped workshop includes 10 heat treatment furnaces, 5 quenching furnaces, 2 central shot blasting machines, and 15 large shot blasting machines.
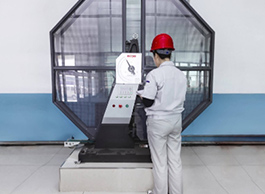
Inspection
All raw casting dimensions are inspected using a CMM (Coordinate Measuring Machine). We also utilize Rockwell hardness testers, dynamic balancing machines, and roundness testers. Our certified quality control team conducts UT (Ultrasonic Testing), PT (Penetrant Testing), and MT (Magnetic Particle Testing) to ensure product quality.
Alloy Steel Sand Casting
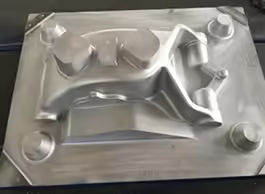
Mold Development
Molds are designed and manufactured according to drawing requirements for alloy steel castings. For single-piece production, wooden molds can be used, while plastic or metal molds are preferred for mass production of alloy steel castings. For high-volume casting, templates are utilized. Our molds are primarily made from aluminum.
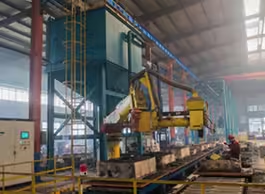
Modeling (Core Making)
This process includes:
Molding – Creating the mold cavity using molding sand.
Core Making – Forming the internal shape of the casting.
Assembly – Placing the core into the mold cavity and sealing the upper and lower sandboxes.
Molding is a crucial step in the casting process.
Molding – Creating the mold cavity using molding sand.
Core Making – Forming the internal shape of the casting.
Assembly – Placing the core into the mold cavity and sealing the upper and lower sandboxes.
Molding is a crucial step in the casting process.
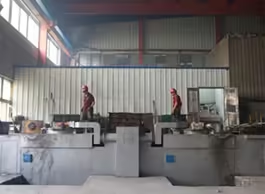
Melting
Based on the required metal composition for alloy steel castings, a chemical composition analysis is conducted. The appropriate melting furnace is selected to melt alloy materials into a qualified liquid metal with the correct composition and temperature for alloy steel castings.
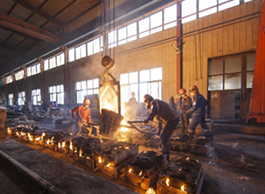
Metal Pouring
The qualified molten metal for alloy steel castings is poured into the sand mold within the sandbox. Since the pouring stage involves high safety risks, we enforce strict process controls to ensure the safety of our employees during the production of alloy steel castings.
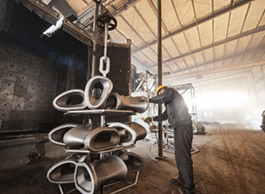
Cleaning & Heat Treatment
Once the molten metal has been poured and solidified, the sand mold is removed, and excess materials such as gates and risers are cleaned off to form the final casting.
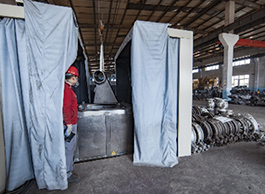
Inspection
All raw casting dimensions are inspected using a CMM (Coordinate Measuring Machine). We also utilize Rockwell hardness testers, dynamic balancing machines, and roundness testers. Our certified quality control team conducts UT (Ultrasonic Testing), PT (Penetrant Testing), and MT (Magnetic Particle Testing) to ensure product quality.
Customizable Surface Treatment Options
Shot Blasting
Shot blasting is a highly effective surface treatment process that involves propelling abrasive materials at high speeds to remove surface contaminants, scale, or rust. This process not only cleans the surface but also improves its adhesion for subsequent coatings. Additionally, shot blasting enhances fatigue resistance, making it ideal for alloy steel castings used in high-stress applications.
Machining
Machining is a precision process used to achieve tight tolerances and smooth surface finishes on alloy steel castings. It includes operations such as milling, turning, drilling, and grinding, ensuring that the final product meets specific dimensional and functional requirements. Our advanced machining capabilities allow us to deliver alloy steel castings with exceptional accuracy and quality.
Paint Coating
Paint coating provides both protective and decorative finishes to alloy steel surfaces. This process enhances corrosion resistance while offering a variety of color and texture options. Whether for aesthetic appeal or functional requirements, paint coating is a versatile solution for alloy steel castings used in various industries.
Powder Coating
Powder coating is a dry finishing process that creates a durable, wear-resistant, and corrosion-resistant surface. This method ensures a uniform appearance and is available in a wide range of colors and textures. Powder coating is particularly suitable for alloy steel castings exposed to harsh environments or requiring long-lasting protection.
Galvanized Coating
Galvanization involves applying a layer of zinc to the steel surface, offering excellent corrosion protection. Hot-dip galvanizing and electro-galvanizing are common methods used to extend the lifespan of steel components.
Black Oxide Coating
Black oxide treatment creates a thin, black protective layer on the steel surface to improve corrosion resistance and reduce light reflection. It is commonly used in automotive, aerospace, and tooling applications.
Start Your Project with Leierwo
1. Submit Your Inquiry
Send your CAD drawings and 3D files via email, specifying material grade, order quantity, surface finish, or any other relevant details.
2. Cost Calculation
Once we receive your design, our engineering team will carefully evaluate the drawings and calculate the price based on actual production costs as soon as possible.
3. Start Production
Upon pricing approval, our production team will prepare the materials and schedule production promptly. Leierwo always ensures on-time delivery.
4. Arrange Delivery
After production is completed, we will provide packaging details and arrange shipment via sea or air. We support global shipping for every order.
FAQ
Do you offer export services?
Can you produce custom-designed alloy steel castings?
What are the size and weight ranges for alloy steel castings?
What international standards do your alloy steel castings comply with?
How do you ensure product quality?
What is your Minimum Order Quantity (MOQ)?
What is your lead time?
Can you provide samples?