Carbon Steel Casting
With excellent mechanical properties, carbon steel castings are more cost-effective than stainless steel castings, offering a perfect balance of performance and affordability. The carbon content is a key factor in determining the toughness of steel. After heat treatment, higher carbon content makes the steel stronger and more wear-resistant, making it the preferred choice for demanding industries such as construction, mining, and heavy machinery.
As an experienced carbon steel casting manufacturer, we specialize in producing high-quality carbon steel castings with superior strength, toughness, and wear resistance. Our advanced production processes and rigorous quality control ensure that each casting meets industry standards and delivers outstanding performance. Whether for industrial equipment, automotive components, or structural applications, our carbon steel castings provide reliable and durable solutions tailored to meet the needs of our clients.
As an experienced carbon steel casting manufacturer, we specialize in producing high-quality carbon steel castings with superior strength, toughness, and wear resistance. Our advanced production processes and rigorous quality control ensure that each casting meets industry standards and delivers outstanding performance. Whether for industrial equipment, automotive components, or structural applications, our carbon steel castings provide reliable and durable solutions tailored to meet the needs of our clients.
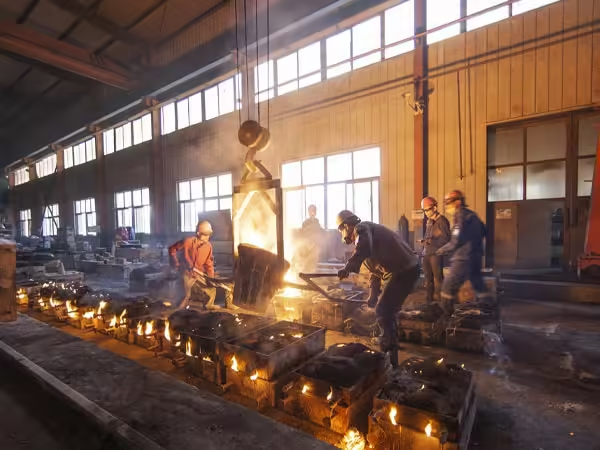
Common Carbon Steel Grades for Casting
Here are the most common carbon steel casting grades. As experts in steel casting, we have extensive experience in producing all carbon steel grades.
Carbon Steel Grade | Description | Application |
---|---|---|
1018 | Low carbon steel, high strength, good ductility, good weldability | Crimping, bending, forging, worm gears, pins, gears, ratchets, etc. |
1020 | Suitable for surface hardening, high carbon steel, hardening and welding | Hydraulic shafts, motor shafts, pump shafts, mechanical parts |
1030 | High carbon steel, moderate hardness, high strength, machinable, good ductility | Mechanical parts, used in tempered and quenched conditions to increase strength |
1035 | Low carbon steel, suitable for induction and flame hardening | Forged parts, connecting rods, gears, couplings, forged shafts, and axles |
1040 | Good strength, wear resistance, high carbon steel | Forged couplings and crankshafts |
1045 | Low carbon steel, suitable for forging, most common shaft steel | Induction hardened applications, medium strength components, pneumatic and hydraulic cylinder shafts |
1050 | High carbon steel, easy to weld and machine | Forged shafts and gears |
1060 | Standard grade carbon steel | Used in forging applications |
1065 | High carbon steel, high tensile strength, heat treatable | Blades and cutlery |
1144 | Low carbon steel, stronger alloy than A36 and 1018, better ductility | Parts requiring mechanical properties obtained by heat treatment |
11L14 | High carbon steel, enhanced machinability, higher strength than 1018 | Forging applications |
12L14 | High carbon steel, enhanced machinability, higher strength than 1018 | Screw machines, couplings, inserts, bushings, hydraulic hose fittings |
Available Carbon Steel Casting Processes
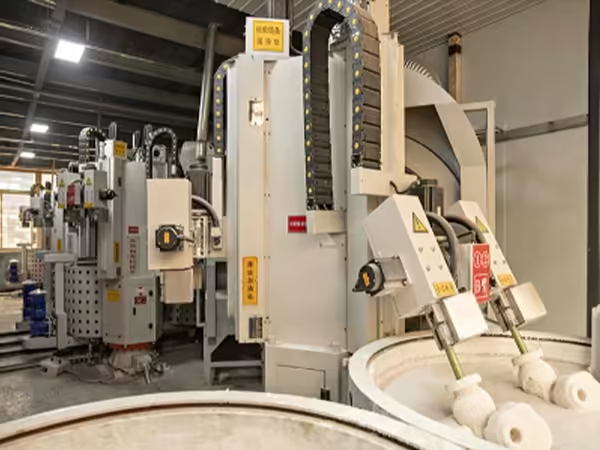
Carbon Steel Investment Casting
Carbon steel investment casting uses the traditional lost wax casting process to produce carbon steel components. In recent years, we have undertaken extensive upgrades, incorporating advanced silica sol shell-making technology. Additionally, we have introduced an innovative process that combines coated sand with shell-making, optimizing production time and improving surface finish. Common carbon steel investment casting parts include railway components and automotive parts.
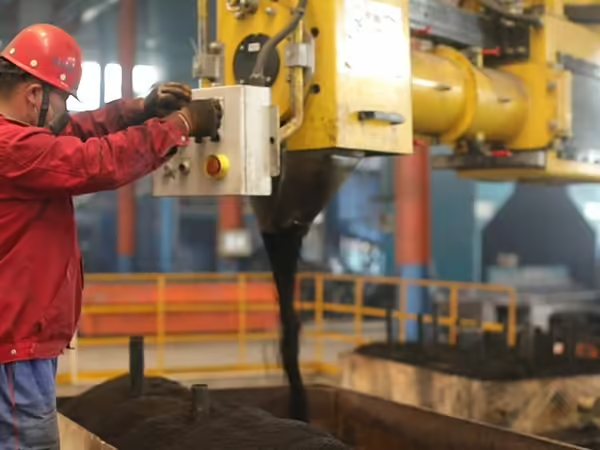
Carbon Steel Sand Casting
Carbon steel castings produced using the sand casting process are known as carbon steel sand castings. In this process, different foundries select various sand materials based on performance requirements, such as silica sand, resin sand, ceramic sand, and expandable sand. We primarily use resin sand and ceramic sand, both known for their uniform granularity and excellent refractory properties, making them ideal for high-temperature, high-performance casting applications.
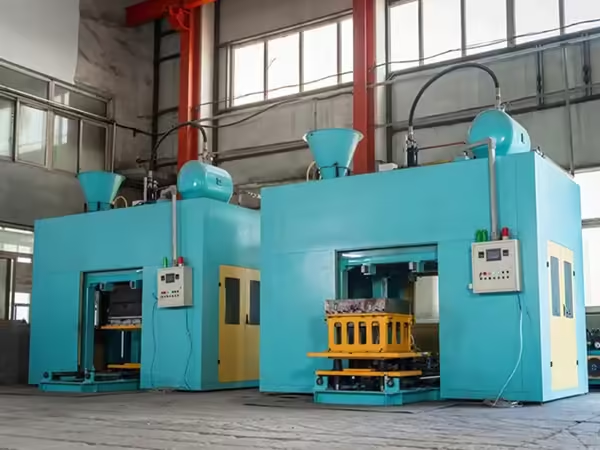
Carbon Steel Shell Casting
Carbon steel shell casting is an advanced shell molding process used to produce high-quality carbon steel components. Our fully automated production line ensures efficiency and consistent quality, with a monthly capacity of 800 tons and the ability to manufacture castings weighing up to 200 kg. This process delivers precise dimensions, excellent surface finishes, and intricate designs, making it ideal for industries such as automotive, construction, and heavy machinery. We provide durable, reliable, and cost-effective carbon steel shell castings tailored to meet the diverse needs of our clients.
One-Stop Solution
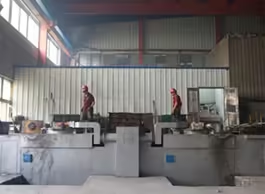
Carbon Steel Casting Cleaning
Carbon steel investment casting, also known as lost wax casting, is a precision casting process that uses wax patterns to create high-accuracy, intricate shapes. This method provides excellent surface finish, tight tolerances, and minimal post-processing, making it ideal for complex components in automotive, aerospace, and industrial machinery. After casting, thorough cleaning is essential to remove any residual mold materials, scale, or impurities. Our cleaning process ensures that each carbon steel casting meets the highest standards of quality and readiness for further treatment or assembly.
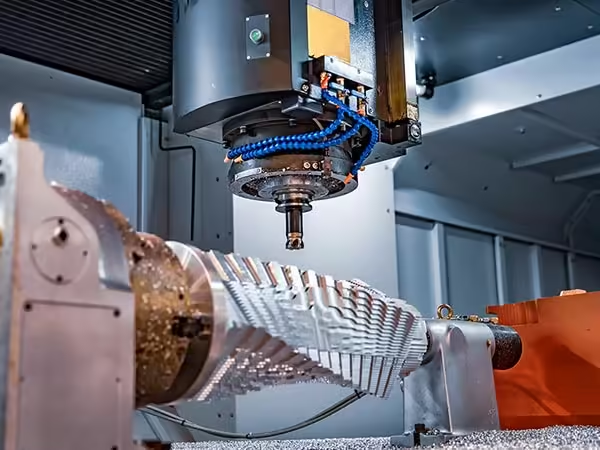
Carbon Steel Casting Machining
Our machining facility houses over 30 CNC machines, providing exceptional flexibility for machining carbon steel castings according to customer drawings. Our skilled technicians, with years of experience, ensure high precision and efficiency in every operation. By maintaining in-house machining capabilities, we reduce the complexity of working with multiple suppliers and minimize lead times. Whether it’s turning, milling, drilling, or grinding, we deliver carbon steel castings with exact specifications and superior surface finishes, ready for immediate use.
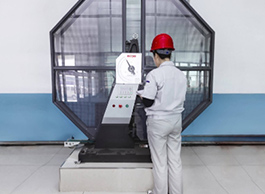
Carbon Steel Casting Inspection
Quality assurance is a critical part of our process. We employ various inspection methods, including dimensional checks using CMM (Coordinate Measuring Machine), visual inspections, and non-destructive testing (NDT) techniques like ultrasonic and magnetic particle testing. These methods ensure that every carbon steel casting meets the required specifications and performance standards. Additionally, we apply surface treatments such as rust-proof oil coating, painting, sandblasting, chemical treatment, anodizing, and electrophoresis to achieve corrosion resistance, enhance wear resistance, and improve appearance. Our rigorous inspection and treatment processes guarantee that our carbon steel castings deliver reliability and durability in even the most demanding applications.
Customizable Surface Treatment Options
Shot Blasting
Shot blasting is a surface treatment process that involves propelling abrasive materials at high speeds to remove surface contaminants, scale, or rust. This process enhances surface adhesion for subsequent coatings and improves fatigue resistance.
Machining
Machining is a precision process used to achieve tight tolerances and smooth surface finishes. It includes milling, turning, drilling, and grinding to meet specific dimensional and functional requirements.
Paint Coating
Paint coating provides a protective and decorative finish to alloy steel surfaces. It enhances corrosion resistance and allows for various color and texture options, making it ideal for aesthetic and functional purposes.
Powder Coating
Powder coating is a dry finishing process that creates a durable, wear-resistant, and corrosion-resistant surface. It offers a uniform appearance and is available in a variety of colors and textures.
Galvanized Coating
Galvanization involves applying a layer of zinc to the steel surface, offering excellent corrosion protection. Hot-dip galvanizing and electro-galvanizing are common methods used to extend the lifespan of steel components.
Black Oxide Coating
Black oxide treatment creates a thin, black protective layer on the steel surface to improve corrosion resistance and reduce light reflection. It is commonly used in automotive, aerospace, and tooling applications.
Start Your Project with Leierwo
1. Submit Your Inquiry
Send your CAD drawings and 3D files via email, specifying material grade, order quantity, surface finish, or any other relevant details.
2. Cost Calculation
Once we receive your design, our engineering team will carefully evaluate the drawings and calculate the price based on actual production costs as soon as possible.
3. Start Production
Upon pricing approval, our production team will prepare the materials and schedule production promptly. Leierwo always ensures on-time delivery.
4. Arrange Delivery
After production is completed, we will provide packaging details and arrange shipment via sea or air. We support global shipping for every order.
FAQ
Do you offer export services?
Can you produce custom-designed Carbon Steel Casting?
Is it expensive to order carbon steel castings from Leierwo Foundry?
What international standards do your carbon steel castings comply with?
How do we ensure product quality?
What is your Minimum Order Quantity (MOQ)?
What is your lead time?
Can you provide samples?