High-Quality Cast Pump Bodies – Durable & Precision Engineered
Shanghai Leierwo Casting Co., Ltd. has over 18 years of experience in casting, providing high-quality products to customers. We specialize in manufacturing custom pump components using various metal materials. Whether it’s pump bodies, volutes, or other pump products, we can cast them to meet your specifications. Feel free to contact us. As one of the best casting manufacturers in China, we look forward to working with you.
Types of Pump Castings
We provide cast pump bodies, pump casings, impeller castings, and other pump castings used in the oilfield, oil extraction and refining, petrochemical, water treatment industries, solid waste management, concrete construction, and more.
Check the following categories of cast pumps to learn more about our pump casting capabilities. Please contact us for your OEM casting pump orders and to receive quotes for each product.
Check the following categories of cast pumps to learn more about our pump casting capabilities. Please contact us for your OEM casting pump orders and to receive quotes for each product.
Our Pump Casting Capabilities
Pump Casting Manufacturer: Pressure Testing and Non-Destructive Testing
We ensure that our pump castings undergo pressure testing. We also perform non-destructive testing (NDT) to verify the integrity of the products. We guarantee that all products we manufacture are leak-free. Additionally, our silica sol casting process ensures excellent surface finish and dimensional accuracy. This allows us to meet the drawing requirements through casting alone, eliminating the need for additional machining. This provides our customers with unparalleled surface treatment and ensures top-notch quality.
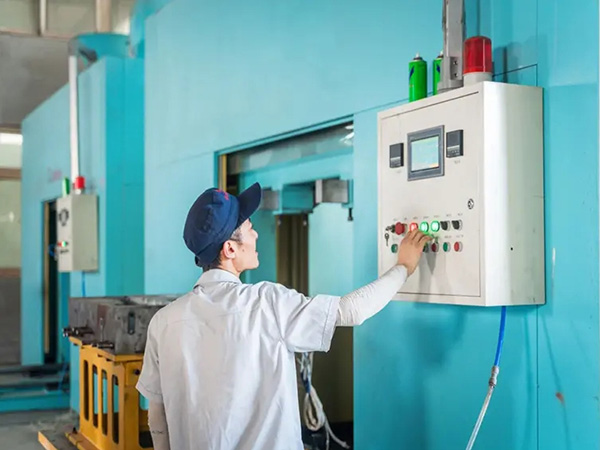

Our Pump Casting Supply Capability
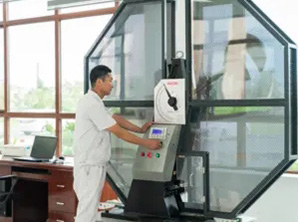
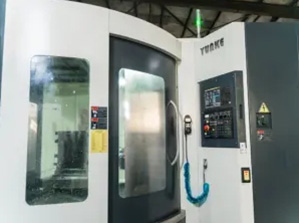
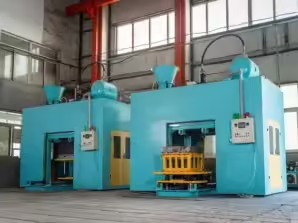
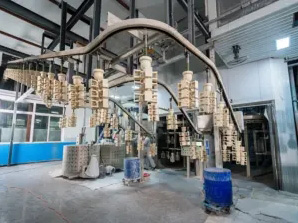
FAQ
Do you offer export services?
Why choose leierwo foundry for casting?
What is your production capacity? Do you accept custom orders?
What international standards do your castings comply with?
How do you ensure product quality?
What is your Minimum Order Quantity (MOQ)?
What is your lead time?
Can you provide samples?